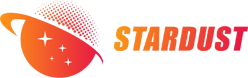
The Swedish chemist Anders Ekeberg first extracted element 73 - tantalum - from a mineral in 1802, and tantalum was named after its excellent corrosion resistance in acids [1]. Tantalum has superior corrosion resistance to titanium [2-4], is only affected by strong acidic and alkaline environments, and remains relatively inert in the human body [5], thus avoiding interference with biological tissues [1]. By forming bone-like apatite layers in simulated body fluids, tantalum has been shown to be biologically active and to biobind to bone [6]. In addition, pure tantalum and its major oxides, both of which have low solubility and toxicity [7], have been used clinically since 1940 and are widely used in diagnostic and implant applications with significant overall results [8]. Excellent biocompatibility and safety have been shown in orthopaedic, craniofacial and dental related studies [9], and the use of dense tantalum metal implants for osseointegration has been demonstrated to be used for up to 8-12 years [10].
The trend in orthopaedic implants has gradually shifted from fixation to bone by means of cement, mechanical fixation devices and surface attachment to biological fixation by means of osseointegration or bone ingrowth [11-12]. Implantation of porous tantalum into the body provides immediate weight bearing and supports bone deep into the internal structures for good long term fixation [13] and a long term postoperative follow-up study demonstrated a 96% survival rate of porous tantalum acetabular prostheses at year 11 [14].BALLA et al [6] found that porous tantalum showed excellent cell adhesion in MTT analysis and immunochemical studies when compared to porous titanium controls, growth and differentiation, the formation of a rich extracellular matrix on porous tantalum, and a six times higher density of viable cells on the surface compared to the titanium surface.WAUTHLE et al [15] found that porous tantalum has excellent osteoconductive properties, higher normalised fatigue strength and allows more plastic deformation due to its high ductility compared to porous titanium alloys of the same process and structure. Clinical studies have shown that utilising the inward bone growth properties of porous tantalum with suitable structures to achieve stable support and bonding capabilities is an effective way of reconstructing bone defects as the severity and duration of the defect increases [16]. The advantages of porous tantalum implants can be summarised as follows:1) The material has excellent corrosion resistance and biocompatibility.2) Body-matched modulus to avoid stress shielding.3) High surface friction characteristics for improved initial stability.4) Adequate mechanical support and long fatigue life.5) Mimics the mass transport properties of bone to support osteoblast attachment, proliferation, differentiation and mineralisation, possessing excellent osteointegration properties [6,17-18].
The preparation of tantalum as a porous implant requires a reduction in its elastic modulus from 185 GPa to around 3 GPa by increasing the porosity to achieve similarity to human bone (0.4 GPa in trabecular bone to 17.9 GPa in cortical bone) [19-20]. Tantalum is a refractory metallic material with a melting point as high as 2996 °C, and under high melting point, tantalum has high affinity for oxygen and other interstitial elements, so the preparation of porous tantalum with high porosity has a certain technological threshold, and chemical vapour deposition (CVD), powder metallurgy (PM), and additive manufacturing (AM) are the main preparation techniques at present (see Fig. 1 [21-23]).CVD is a complicated and high-cost traditional manufacturing process, porous tantalum implants with patient-specific anatomical features cannot be easily customised, and there are some limitations in the design of the porous structure.PM, although less costly, prepares porous tantalum with lower porosity, uneven pore sizes and high closed porosity, and prominent problems such as internal connectivity, which affects the osteogenic performance of porous tantalum implants. However, a stable and controllable porous structure with high connectivity is an important factor for cell migration, adhesion and proliferation. Therefore, porous tantalum implants prepared using additive manufacturing technology have a controllable and designable pore structure, which is suitable for personalised precision medicine, especially in complex bone defects caused by trauma or tumour resection. Scholars have long believed that the application of tantalum is limited by processing technology rather than biological properties [6,8,24], and relatively high manufacturing costs and quality control difficulties have limited the widespread acceptance of porous tantalum, but emerging metal additive manufacturing is gradually lifting this limitation, and allows for a more flexible and free design of porous tantalum implants in terms of form factor, internal porous structure, and properties, which has greatly facilitated the application of tantalum metal as a biomedical material. medical materials.
Fig. 1 Main preparation techniques of porous tantalum implants[21-23]
In the additive manufacturing process of porous tantalum implants, from model design, raw materials, equipment to forming process and post-processing will affect the quality of porous tantalum, and the related regulatory science and common technology research work urgently needs to be promoted in a concerted manner. Combined with the actual production, the authors' team summarises the current bottlenecks and difficulties in the preparation of additive manufacturing porous tantalum as follows: 1) In terms of raw materials, the high cost of medical spherical tantalum powder, the low number of times it can be recycled, the lack of research on the key properties of tantalum powder directly affecting the quality of additive manufacturing porous tantalum and the lack of research on the intermediate properties (e.g., spreading properties, humidity), etc., the difficulty and the cost of systematically verifying and controlling the effect of raw material spherical tantalum powder on the physicochemical properties of additive manufacturing porous tantalum. 2) In terms of defect formation, the extremely high cooling rate and non-equilibrium solidification during the additive manufacturing process lead to a variety of uncontrollable defects in porous tantalum, and the defects induced by different process conditions and different levels of interstitial impurity elements differ in shape, size and distribution [25-28]. aliyu et al. [26] studied the formation mechanism of the defects in additively manufactured porous tantalum, including the formation mechanism of the defects in porous tantalum, and the formation of the defects in porous tantalum. defect formation mechanisms, including solidification-induced microporosity, pore-induced microcracking and solidification-induced microcracking, as well as the dislodging of incompletely melted tantalum powder particles from porous tantalum surfaces during post-processing led to the generation of micro-pit and micro-groove defects. Distinguished from other technologies, micro-pit and micro-groove defects have a detrimental effect on the mechanical and biological properties of porous tantalum implants that are currently directly applied to the human body, which is reflected in the absence of local edge positions of porous tantalum wire rods, which are more prone to failure under load.3) In terms of porous tantalum implant particles residue, due to incomplete tantalum powder melting, tantalum powder powder adhesion exists on the surface of porous tantalum wire rods, which is currently lacking in the additive manufacturing porous tantalum cleaning process research, if the removal of tantalum powder particles is not complete, porous tantalum products after implantation in the human body, there is the possibility of particle dislodgement, which will lead to a significant increase in the risk of complications, and also the same impact on the safety and effectiveness of the product [29].
In this paper, the authors reviewed the progress related to the raw materials, preparation technology, mechanical study, ex vivo evaluation and clinical application of additively manufactured porous tantalum, and put forward the future outlook of additively manufactured porous tantalum in combination with the team's many years of research work in customised additively manufactured tantalum metal implants.
1 Raw materials for additively manufactured porous tantalum
Currently, the mainstream porous tantalum additive manufacturing process is powder bed melting, and its raw material is medical spherical tantalum powder in the range of 15~150μm particle size. With the maturity of additive manufacturing equipment and the increased demand for personalized porous tantalum implants, from 2015, research institutions and powder manufacturing enterprises in various countries have carried out the development of the spherical tantalum powder process [30], which has been well controlled in terms of the sphericity of the tantalum powder, the fluidity, the bulk density, the high vibration density, and the rate of hollow powder, etc., and at present, its main preparation technologies are plasma spheronisation (PS) and plasma rotating electrode atomisation (PREP) (see Figure 2 [30-31]). Changes in the initial state of tantalum powder and in the properties of the powder during recycling have a direct impact on the quality of porous tantalum. The quality control measures of tantalum powder and its recycling are one of the technical elements to be considered in the medical device certification process [32]. Currently, YY/T1851-2022 and GB/T38975-2020 are commonly used as acceptable standards for evaluating tantalum powder for powder bed fusion process [33-34].
The principle of PS technology is that high-temperature plasma melts the surface/whole of irregular tantalum powder transported by the carrier gas, and then it condenses into spherical droplets under the action of surface tension, and solidifies into powder in a cooling chamber [31].The raw material used in the PS technology is tantalum powder, and the investment in equipment is large, and the operating costs are high, so the overall cost of preparing spherical tantalum powder is high. Although PS technology spheroidisation is effective, the spheroidisation efficiency is low as well as oxygen contamination is prone to occur during the spheroidisation process.QIN et al [35] reported the existence of a small number of irregular and rough surface particles of spherical tantalum powder prepared by PS technology, and argon was used to protect them during the preparation process, but the oxygen contamination still occurred, and the energy spectroscopy analysis showed that there was an oxide film on the surface of the tantalum powder particles, and the internal oxygen content of the particles was low. Further, HAO et al [36] investigated the effect of raw materials for different processes and process parameters such as carrier gas flow rate, powder feeding rate and secondary spheroidisation on spheroidal tantalum powder, and the results showed that hydrodehydrogenated tantalum powder is more suitable for PS technology than sodium-reduced tantalum powder. The quality of spherical tantalum powder is ultimately reflected in the quality of additive manufacturing tantalum formers, the oxygen content of tantalum powder is an important factor affecting the microstructure and mechanical properties of additive manufacturing tantalum formers.SUNGAIL et al [37] prepared high and low oxygen content tantalum powder formers and carried out microstructural observation and mechanical property tests, the results show that the oxygen content of tantalum powder with low oxygen content (87 × 10-6 ) formers with low oxygen content (107 × 10-6 ) and low oxygen content (107 × 10-6 ) are more suitable for PS technology. low oxygen content (107 × 10-6 ), with high elongation and tensile strength (35%, 634 MPa), and the tensile fracture mode was ductile fracture.SHI et al [38] used 481 × 10-6 tantalum powder to prepare the formed parts with a maximum tensile strength of 697 MPa, and the elongation rate was 28.5%. Tantalum powders prepared by fluidisation, air flow milling (JM) and PS techniques, and found that due to the low oxygen content of tantalum powders prepared by JM and PS techniques, the formed parts showed good precision and low hardness.TAN et al [40] investigated the effect of oxygen content of tantalum powders on the additive manufacturing process, microstructure, and mechanical properties, and the results showed that the process window of tantalum powders with low oxygen content was larger, and with the increase of the oxygen content (150×10-6→470×10-6), the formed parts were more precise than the formed parts, with the increase of the oxygen content (150×10-6→470×10-6). 10-6), the grain structure of the formed parts changed from {100}||BD to {111}||BD and the ultimate tensile strength increased (391 MP (42% → 29%). The difference between the findings of SUNGAIL and TAN on the elongation of the formed parts may be influenced by the study interval of the oxygen content of tantalum powder (SUNGAIL: 87 × 10-6~829 × 10-6, TAN: 150 × 10-6~470 × 10-6), the forming equipment and the process.
Fig. 2 The main preparation technologies and difficulties of spherical tantalum powder for medical additive manufacturing
The principle of PREP technology is that high-temperature plasma melts the end face of the tantalum rods of the self-consuming electrodes rotating at high speed, and the molten liquid film is broken into micro-droplets under the effect of centrifugal force and solidified into powder [31], compared with PS technology, PREP technology is based on high-purity tantalum rods as raw materials, which has obvious advantages in the cost of production, the control of powder morphology and the content of impurities [30]. However, the yield of spherical tantalum powder below 45 μm prepared by PREP technology is low, generally less than 10%. Therefore, improving the fine powder yield of PREP tantalum powder is the main challenge for this technology in the field of porous tantalum additive manufacturing.
In addition to the previous focus on additive manufacturing process parameters, recent studies have shown that factors such as the content of interstitial impurity elements in tantalum powder have a significant impact on the biological properties of porous tantalum, the stability of the additive manufacturing process and the quality of the subsequent implant. On the one hand, interstitial impurity elements such as oxygen have a strong solid solution strengthening effect on BCC-structured tantalum, which has a significant effect on the toughness of tantalum [41], and a small amount of interstitial oxygen atoms is beneficial to the improvement of tantalum toughness [42]. On the other hand, the increase in oxygen content reduces the wetting and diffusion ability of the melt and hinders the connection of the melt pool, leading to partial melt pool instability [40]. The densities of low-oxygen tantalum powder (150 × 10-6 ) formed parts were insensitive to the laser energy density, whereas the high-oxygen tantalum powder (470 × 10-6 ) formed parts still showed an increase in the number of pore defects and larger sizes under the optimised process parameter conditions [40], which suggests that the increase in the oxygen content resulted in a narrower process window. As the initial oxygen content of tantalum powder increased, along-crystal fracture was observed in the samples with an oxygen content of about 510 × 10-6 at the fracture location, and due to the enrichment of oxygen elements at the grain boundaries [41], the main fracture mode was changed from the typical ductile fracture to a combined fracture mode of brittle and ductile fracture [37]. Tantalum powder impurity elemental oxygen mainly originates from gases encapsulated in the powder [41]. According to the above domestic and international studies [31, 37-38], with the increase of oxygen content in the raw tantalum powder, the oxygen increment of tantalum for additive manufacturing shows an overall increasing trend, which is mainly due to the following two reasons: 1) The increase of oxygen content (oxides) in the raw tantalum powder leads to a higher melting energy required, and the long residence time of the melt pool under the action of the high energy density results in a slower solidification speed, and the diffusion of the surface oxygen to the inside of tantalum formed parts takes a time becomes longer.2) Marangoni convection is more pronounced, leading to an increase in the contact area of the sputtered tantalum powder particles with the oxygen impurities in the forming chamber atmosphere.LEI et al [43] showed that ex vivo and in vivo tests showed better bone formation due to the low contact angle of low-oxygen tantalum water. Therefore, tantalum powder with too high oxygen content is not favourable for the preparation process and clinical application of additively manufactured porous tantalum (see Figure 3 [35,40,42]).
Tantalum powder is relatively expensive and recycling it in the additive manufacturing process can reduce the cost. Metal powder recycling is a process state unique to additive manufacturing technologies that use metal powder as a raw material, and recycling can greatly improve powder utilisation. Additive manufacturing forming environment, powder recycling, sieving, drying, mixing, storage and other aspects of the process of multiple use may introduce impurity elements, which will have a certain impact on the quality of the powder. The Guiding Principles for Research on the Homogeneity of Physicochemical Properties of Additively Manufactured Metal Implants (No. 4, 2022) mention the need to validate the impact of recycled powder on the homogeneity of the printing process and product quality. In order to validate the number of times tantalum powder can be recycled, the authors' team systematically investigated the change of powder properties during the recycling process of additively manufactured tantalum powder and its impact on the quality of tantalum formed parts [44]. In terms of powder properties, as the number of tantalum powder recycling times increased, the oxygen content of tantalum powder gradually increased from 46 × 10-6 initially to 180 × 10-6 in 30 furnaces of recycling. due to the forming in a vacuum environment, the oxygen increment of tantalum powder in a single furnace was only 4.7 × 10-6 on average, and the particle size of tantalum powder slightly increased due to spattering, adherence, and remelting in the process of forming and due to the sintering connection, crushing recovery of the powder particles during the recycling process. Due to the sintering connection and crushing and recycling of the powder particles in the recycling process, the surface morphology of the powder particles became incomplete, so the fluidity decreased slightly, but the bulk density and vibration density did not change significantly. In terms of the properties of the formed parts, the following conclusions were made under the same process parameters: 1) The study of solid tantalum showed that there was no introduction of impurities during the reuse of tantalum powder, with a decreasing trend in the densification, and no significant change in the tensile strength, whereas the elongation decreased with the increase in the number of times of reuse, with a decrease in elongation of 34.7 per cent after 30 times of reuse. 2) The study of porous tantalum showed that, after 30 times of reuse of the tantalum powder, the porous tantalum porosity remained stable, but the surface spheroidisation increased (see Fig. 4 [44]), and the compressive yield strength and plateau stress both decreased by about 20%. Taken together, it is particularly critical to pay attention to the oxygen content of the raw material tantalum powder in the additive manufacturing process of porous tantalum.
Fig. 3 Oxygen content of tantalum powder affects biocompatibility, process window and mechanical properties of additive manufacturing porous tantalum
Fig. 4 Effects of reuse 30 times on surfaces of tantalum powders and additively manufactured porous tantalum[44]
2 Additive Manufacturing of Porous Tantalum
In clinical treatment, through medical-industrial interaction, additive manufacturing technology can be used to precisely customise orthopaedic implants with patient-specific anatomical features, and at the same time, the pore structure parameters of different regions of the implant can be customised to meet the elasticity modulus requirements of human bone tissues and avoid the phenomenon of stress shielding. Additive manufacturing is a process of manufacturing parts or physical objects by stacking materials based on 3D model data. According to the technical principles, GB/T35021-2018 and ISO/ASTM52900:2023 classify the current additive manufacturing technologies into seven categories [45-46]. Among them, the selective laser/electron beam melting technology (SLM/EBM) is the most widely used technology in the additive manufacturing of metallic orthopaedic implants due to its advantages of high precision, high efficiency, and good stability, and it belongs to the powder bed fusion process (PBF) in the classification.
2.1 SLM technology
The process flow and technical principle of preparing porous tantalum implants using SLM technology is shown in Fig. 5 [13,44,47], where a high-energy laser beam with suitable parameters in the additive device selectively melts the tantalum powder laid on the substrate, and porous tantalum shaped parts with controllable apertures are fabricated layer by layer according to the data of the porous structure model, and the whole shaping process is carried out in a protective atmosphere to avoid oxidisation, and the shaped parts are used to be The porous tantalum molded parts are cut from the substrate using a cutting machine, and the unmelted powder inside the porous tantalum molded parts is removed by sand blasting and other processes, and then the molded parts are annealed to eliminate the residual stresses generated during processing, and the final porous tantalum implant is obtained by cleaning and sterilisation and packaging. During the preparation process, the porous structure model data is obtained by engineers who design the implant and process the model prior to printing.
The particle size range of the raw material tantalum powder suitable for SLM technology is typically 15-53 μm.
During SLM forming of tantalum metal, complex thermal processes lead to differences in the microstructure of tantalum formed parts with different morphologies [22,48-53]: 1) Directional melting and rapid solidification due to thermal inputs at different process parameters. 2) Scanning strategy. 3) Partial remelting of the previous deposited layer. 4) Differences in the thermal conductivity of the substrate material, as well as substrate-induced specific directions of the heat flow, etc. SLM Forming The microstructure of bulk dense tantalum usually has strongly columnar grains along the forming direction, with an average grain size of about 54.7 μm, which is larger than the average grain size of conventionally forged tantalum (about 18.9 μm) (see Fig. 6(a) and (c) [54]).The grain shape of SLM porous tantalum is close to that of SLM bulk dense tantalum, and since the filament diameter of porous tantalum is usually in the range of several hundreds of micrometres, the heat diffuses into the powder more readily, the The grain size is closer to that of wrought tantalum (see Fig. 6(b) [55]).