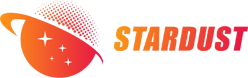
Ta-10W alloy is a rare metal alloy material with high density, high melting point and high strength. It has high high temperature strength, good ductility, weldability and excellent corrosion resistance. It is suitable for high temperature, high pressure and Corrosion and other working environments, according to information [1, 2]: Ta-10W alloy can be used at 2500°C. The combustion chamber of the American Agena spacecraft and the nose cone of the missile engine are made of Ta-10W alloy. Tungsten forms an alternative continuous solid solution with tantalum in tantalum. Tungsten mainly plays a solid solution strengthening effect on tantalum, significantly improving the mechanical properties of tantalum metal. Since Ta-10W alloy is often used to make key or important parts in high-temperature environments, its high-temperature properties, especially its failure mode at high temperatures, are important properties that have attracted much attention. This article focuses on the fracture morphology of samples after high-temperature tensile properties testing of Ta-10W alloy from 1000 to 2000°C, and discusses the plastic deformation mechanism of the alloy at high temperatures.
1 experiment
The Ta-10W alloy rod used in the test is an ingot that has been secondary melted by vacuum electron beam (ingot size Φ97.5mm). It has been processed by hot die forging and cold drawing to Φ14mm, then vacuum recrystallization annealing, and then turning. into a sample. The metallographic structure of the sample is shown in Figure 1, and the chemical composition of the materials used in the test is shown in Table 1.
The processed sample is shown in Figure 2. The sample for high-temperature mechanical property test is different from the sample at normal temperature. The high-temperature mechanical property test was conducted on the CSS-2220 ultra-high temperature material testing machine, which has a maximum test temperature of 3000°C. Since the specimen is difficult to clamp at high temperatures, both ends of the specimen are threaded. The sample is heated by direct electric heating. The clamp that connects the specimen is also an electrode that is electrically heated. Heating adopts a combination of main heating and auxiliary heating. The main heating is connected to the threaded part of M12. In order to ensure the uniformity of temperature, an auxiliary heating device is installed at the Φ10mm position of the sample. The temperature of the test furnace is measured with a photoelectric colorimetric pyrometer produced in the United States, and three-point temperature measurements are performed within the gauge length of the sample. During the test, first fix the sample on the fixture in the vacuum chamber, evacuate the furnace body, and then fill the furnace body with argon gas for protection. After it is heated to the test temperature, such as 1000°C, a tensile test is performed during insulation until the material breaks. The mechanical properties of the material at this temperature are obtained. Repeat the above process to measure various mechanical properties at 1200, 1400, 1600, 1800 and 2000°C. The test method follows the DqES383-2001 standard, and the tensile speed is 5mm·min-1. The specimens that were broken after testing at each temperature were first marked, and then sampled and prepared respectively. Then, SEM fracture scanning was performed on the CAMEBAX-MICRO614 electronic probe, and metallographic analysis was performed on the MM6 metallographic microscope. Compare with the mechanical property test results of the alloy. After sorting out the data after the mechanical property test, the relationship between the mechanical properties (tensile strength σb, yield strength σp0.2, elastic modulus Et, elongation δ5 and area shrinkage ψ) of Ta-10W rods as a function of temperature was obtained (Figure 3), the metallographic photo is shown in Figure 4.
Figure 1 Metallographic photo of Ta-10W alloy rod
2 results
2. 1 High temperature fracture morphology at 1000℃
The photos of high-temperature fracture morphology at 1000°C are shown in Figure 5. It is a typical equiaxed dimple fracture. The central dimple area is small, and the dimples are very small and shallow in depth, indicating that the material has low plasticity at this temperature [3-5] and the hardening is obvious.
2.2 High temperature fracture morphology at 1200℃
The photos of high-temperature fracture morphology at 1200°C are shown in Figure 6. The dimples at this temperature are larger and deeper than those at 1000°C, indicating that the plasticity of the material increases with the increase of temperature. There are inclusions at the bottom of the dimples (Figure 6(c)), which may become crack sources.
Figure 2 Ta-10W alloy high temperature test specimen (mm)
Figure 3 Ta-10W rod performance changes with temperature
Figure 4 Metallographic structure of Ta-10W alloy after high temperature test
2.3 High temperature fracture morphology at 1400℃
The photos of high-temperature fracture morphology at 1400°C are shown in Figure 7. At this temperature, the dimples continue to grow and deepen, with large and small dimples existing at the same time, and dense small dimples are scattered around the large dimples.
2.4 High temperature fracture morphology at 1600℃
The photos of high-temperature fracture morphology at 1600°C are shown in Figure 8. Two different fracture morphologies appeared. The one on the left is still an ordinary equiaxed dimple, and the dimples continue to grow and deepen. A new type of "dimple" appears on the right. This "dimple" is an annular shape. Appearance. The longitudinal section appears in a relatively regular strip shape (Fig. 8(d)). There are secondary cracks at the bottom of this "dimple". These two different fracture morphologies represent two different forms of deformation. At this time, the elongation of the material reaches the highest point (Figure 3), indicating that these two different types of deformation appear at the same time, further improving the plasticity of the material.
2.5 High temperature fracture morphology at 1800℃
The high temperature fracture morphology at 1800°C is shown in Figure 9. There are still two different forms of fracture morphology coexisting, but these two "dimples" are larger and deeper, and grain-like materials can be seen between the annular ridges (Figure 9 (d), Figure 10 (c)), An electron probe was used to analyze the chemical composition of this micro area, and the results showed that in addition to Ta and W, it also contained elements such as Fe, O, C, and Al, so it may be oxides or carbides formed by these elements at high temperatures. At this time, the material's area shrinkage reached its highest point, and the elongation did not decrease significantly (Figure 3).
Figure 5 High temperature fracture morphology of Ta-10W alloy at 1000℃
Figure 6 High temperature fracture morphology of Ta-10W alloy at 1200℃
Figure 7 High temperature fracture morphology of Ta-10W alloy at 1400℃
Figure 8 High temperature fracture morphology of Ta-10W alloy at 1600℃
Figure 9 High temperature fracture morphology of Ta-10W alloy at 1800℃
Figure 10 High temperature fracture morphology of Ta-10W alloy at 2000℃
2.6 High temperature fracture morphology at 2000℃
The high temperature fracture morphology at 2000°C is shown in Figure 10. The original ordinary dimples disappeared, and only the new annular "dimples" existed alone and occupied the center of the specimen. Inclusions are visible on the annular bottom platform (Figure 10(d)), and the results of electron probe analysis show inclusions of Al and O. At this time, the area shrinkage has not decreased and is still on the highest platform. The elongation is slightly lower than that at 1600°C, and is on the same platform as 1800°C (Figure 3).
3 discussions
We know that the main modes of plastic deformation of polycrystals at room temperature are slip and twinning. Slip and twinning are hindered by grain boundaries. The effects of grain boundaries on polycrystalline plastic deformation can be summarized in the following four aspects: coordination, hindrance, cracking, and high-temperature weakening [6-9]. The grain interface is essentially a lattice transition surface connecting two grains with different orientations. There are usually certain regular lattice irregularities at the grain boundaries. There are a large number of dislocations and point defects on the grain boundaries, and impurity atoms and certain precipitated phases are often preferentially distributed on the grain boundaries. According to the dislocation theory, the grain boundaries themselves can undergo plastic deformation, which has long been proven in practice. However, when deforming at low temperatures and room temperature, since the strength of the grain boundaries is stronger than that of the grains, the slip is mainly concentrated inside the grains, and It is unlikely to pass through the grain interface and proceed inside adjacent grains. The stress field generated by a large number of defects in the grain boundaries makes slipping inside the grains more difficult. This is the hindering effect of the grain boundaries.
But when deforming at high temperatures, the situation changes in the opposite direction. Grain boundaries have the effect of weakening at high temperatures. When deforming at high temperatures, since the grain boundaries are weaker than the grains, in addition to intra-grain slip, two adjacent grains will also slide relative to each other along the grain boundaries, which is called grain boundary sliding. Sometimes grain boundaries also occur. Turn. Grain boundary sliding can also cause macroscopic plastic deformation of crystals, but the amount of deformation is often smaller than the plastic deformation caused by slip and twinning.
Grain boundary sliding is often accompanied by grain boundary migration. The so-called grain boundary migration is the directional movement of atoms in one grain to another grain through diffusion, causing the grain boundary to migrate from one position to another. If the test temperature is very high and the applied stress is very low, plastic deformation caused by the directional diffusion of lattice defects, called diffusion creep, may also occur.
The recrystallization temperature of Ta-10W alloy is usually between 1450 and 1550°C, and processing above this temperature is called hot processing. During hot working, the metal will undergo dynamic recovery and dynamic recrystallization while deforming, and two opposite processes of work hardening and softening will occur at the same time.
Ta-10W alloy has a bcc structure and is a metal with high-level dislocation energy, which is prone to cross-slip. According to general theory, the main mode of softening of Ta-10W alloy during thermal deformation should be dynamic recovery. However, since W and Ta form a substitutional continuous solid solution, W has a high melting point, high diffusion activation energy, and low diffusion rate, which makes cross-slip difficult and the dynamic recovery process will be hindered, making the Ta-10W alloy Dynamic recrystallization tendency increases.
When the Ta-10W alloy is subjected to a tensile test below the recrystallization temperature, since no dynamic recrystallization occurs, the pinning effect of the dislocations by the solid solution strengthening of the alloy controls the plastic deformation of the alloy. The plastic deformation of the alloy mainly relies on It is completed by sliding, so the material shows a general dimple fracture morphology below 1400°C. As the temperature increases, the plastic deformation of the alloy occurs in two opposite processes: work hardening and dynamic recovery softening. The cause of work hardening is the result of dynamic strain aging [10]. Dynamic strain aging is an aging process that occurs when metals and alloys undergo plastic deformation. In essence, dynamic strain aging is the result of the interaction of solute atoms with moving dislocations. The higher the temperature, the more dominant the recovery softening is, and the easier it is for dislocations to cross-slip. Therefore, in the range of 1000~1400℃, as the temperature increases, the plasticity of the alloy becomes better, the strength is lower, and the equiaxed dimples appearing in the fracture become larger and deeper. At the same time, the higher the temperature, the more dynamic the metal becomes. The greater the recovery effect, the better the plasticity of the material.
When the temperature rises above the recrystallization temperature, that is, when it reaches above 1600°C, the material undergoes dynamic recrystallization, further softening the material, and the plasticity of the material reaches its highest point, indicating that dynamic recrystallization contributes greatly to the improvement of material plasticity. At the same time, due to the increase in temperature, the grain boundaries are further weakened, and the plastic deformation mechanism of the material changes. The deformation mechanism dominated by slip at low temperature gradually changes to a high-temperature deformation mechanism dominated by grain boundary sliding. Among them, the coexistence of two deformation mechanisms at 1600 and 1800°C is a strong evidence of this transition. Until reaching 2000°C, the plastic deformation mechanism at low temperature completely disappears, and the plastic deformation is controlled by the grain boundaries at high temperature. The deformation mechanisms are controlled by sliding and rotation, accompanied by grain boundary migration and diffusion creep, which also induce small plastic deformations. As a result of the comprehensive effect, the elongation and area shrinkage of the material at 2000°C are not significantly reduced. It can be seen from the inclusions existing between the bottom of the grain boundary sliding "dimple" and the annular ridge that these inclusions may become the source of cracks in grain boundary sliding. It can be observed from Figure 4 that the grain size after the material test at 1600-2000℃ is slightly larger than the grain size after the material test at 1000-1400℃, which also shows that the material undergoes dynamic recrystallization at higher temperatures.
The plastic deformation caused by grain boundary sliding and rotation at lower temperatures is generally small, so the main mode of plastic deformation at low temperatures is still slip. As the temperature increases, the grain boundaries further weaken and grain boundary sliding occurs. The contribution to plastic deformation gradually increases until the plastic deformation is finally controlled by the deformation mode dominated by grain boundary sliding at high temperature. This is the law of Ta-10W alloy in high temperature plastic deformation.
4 Conclusion
1. As the temperature increases, the plastic deformation mechanism of Ta-10W alloy changes from sliding mainly to grain boundary sliding and rotation.
2. There are two opposite processes of work hardening and dynamic recovery or recrystallization of Ta-10W alloy during high-temperature deformation, and dynamic recrystallization contributes more to plasticity than dynamic recovery.
reference:(c)1994-2024 china Academic Journal Electronic pubolishing House. Al rights reserved. http://www.cnki.net
The spherical Ta10W alloy powder prepared by Stardust Technology using radio frequency plasma spheroidization technology has excellent sphericity, high purity, low oxygen content and good fluidity. This makes it widely used in high-end manufacturing, especially in 3D printing, metal injection molding and other technologies, providing high-quality material support.
If you have spherical tantalum 10 tungsten alloy powder or other rare refractory metal powders, single spherical powders, alloy powders, refractory high entropy alloy powders, you can consult Cathie Zheng (+86 13318326187).