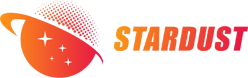
The advantage of additive manufacturing technology (AM) in the field of orthopedic implants is that it can facilitate the creation of anatomically matched devices and surgical instruments by using the patient's own medical imaging data. Another advantage is the ease of manufacturing complex geometries, allowing the creation of engineered porous structures and internal support structures, which is difficult to do easily using traditional manufacturing methods. When the geometry of the patient's bones is not within the specifications of standard-sized implants, or only when a customized solution can bring better clinical results to the patient, the manufacture of customized orthopedic implants through the combination of additive manufacturing and CT or MRI imaging technology can meet specific patient needs and has become an important area of the medical industry. This article mainly introduces the process of additive manufacturing technology and some applications of this technology in the field of orthopedic implants.
I. Introduction to the manufacturing process
(I) Product requirements
The main goal of the manufacturing process of additive manufacturing orthopedic implants is to meet the needs of patients by transferring product requirements into the product. These requirements are limited by each individual clinical case and patient situation, and product functions, geometries, materials, and fixed interfaces must be defined throughout the development process of the product.
(II) Design process
The design process of additively manufactured orthopedic implants is based on the principle of reverse engineering. The process is based on the clinical condition of each patient, using medical imaging technologies such as computed tomography (CT) and magnetic resonance imaging (MRI) to collect imaging data from different angles, and then processed by software algorithms, so that a virtual 3D model can be reconstructed to accurately reflect the patient's condition. For customized prostheses, the subsequent design process requires close cooperation between clinicians and design engineers to use the generated model and the potential clinical situation to design the implant and determine its structural characteristics, such as implant size, material, osteotomy position, and implant-bone fixation method. In addition, a surgical plan needs to be made and corresponding special surgical instruments need to be designed. The AM process itself and subsequent processing processes must also be taken into account, such as the design of support structures and the removal of residual powder.
(III) Production process
In order to ensure the safety and effectiveness of the product, the additive manufacturing process and subsequent processes need to establish good production quality management specifications and fully verify the performance of the product to ensure product quality. At present, domestic and foreign (ISO and ASTM and other standardization organizations) are formulating standards for materials, equipment, environment, process and product verification for additive manufacturing, and some standards have been released.
(IV) Postprocessing
The postprocessing of products must be carried out in a way that meets the previously determined product requirements and undergoes sufficient process verification. The choice of postprocessing depends on the product design, materials and additive manufacturing process, such as heat treatment of metal products to reduce residual stress, removal of residual powder in porous structures, and cleaning of processing aids in subsequent machining processes.
Figure 1 Additive Manufacturing Product Flowchart
II. Application Examples
(I) Knee Prosthesis
Due to the differences in patient anatomical structures, standard-specification knee prostheses may have medial and lateral overhang and undercoverage of the distal femur and rotational malalignment on the tibial side. Standard knee prosthesis products solve such problems by increasing product size specifications and anatomical tibial platforms. Using patient imaging data (CT or MR scans) through proprietary software, knee prostheses and special surgical instruments can be designed to meet the specific patient's knee geometry and anatomical requirements. After the knee prosthesis design model is determined, a wax mold is printed using additive manufacturing technology, and then the wax mold is used to cast the cobalt-chromium-molybdenum femoral component and tibial component of the knee prosthesis. At the same time, special surgical tools are designed based on the surgical plan and the patient's anatomical data, such as guides for alignment, positioning, and osteotomy functions, to reduce the number of tools and trays and simplify the surgical process.
Figure 2 Product design and development process and special surgical tools
(II) Intervertebral fusion cage
Intervertebral fusion cages are used for intervertebral fusion surgery for patients with degenerative disc disease. Their relatively small product size, complex structural design (providing sufficient structural support and bone grafting area), and porous surface structure make additive manufacturing technology a feasible method for producing porous intervertebral fusion cages. Additive manufacturing technology can introduce porous structures into intervertebral fusion cages, which can reduce the elastic modulus and thus reduce stress shielding, and may facilitate bone ingrowth and thus increase stability.
(III) Bone filling block
3D printed bone filling block for ankle internal fixation
Stardust Technology
Stardust Technology (Guangdong) Co., Ltd. is a national high-tech enterprise specializing in the research, development, production and sales of high-end spherical powder materials for 3D printing, powder metallurgy, surface engineering and other fields. The company insists on taking radio frequency plasma spheroidization powder making technology as the core and provides internationally advanced powder products and application solutions.
The company's main products include high-end rare refractory metals such as tungsten, molybdenum, tantalum, niobium, vanadium, rhenium, chromium and their alloys, compound spherical powders. At the same time, it provides technical services such as radio frequency plasma spheroidization, plasma rotating electrode atomization, 3D printing, hot isostatic pressing, injection molding, powder metallurgy, etc.
Medical grade spherical tantalum powder
The spherical tantalum powder produced by Stardust Technology using radio frequency plasma spheroidization technology has excellent biocompatibility and bone ingrowth properties, and is widely used in 3D printing of clinical medical implants such as spine, joints, and trauma. Stardust Technology is the first in China to achieve an industrial breakthrough in medical-grade spherical tantalum powder. It has jointly promoted the clinical medical application of tantalum metal with domestic first-class orthopedic hospitals and medical device companies. It has participated in the formulation of GB/T 38975-2020 Tantalum and tantalum alloy powder for additive manufacturing, GB/T 41883-2022 Powder bed fusion additive manufacturing of tantalum and composite alloys related national standards, YY/T1851-2022 Medical pure tantalum powder for additive manufacturing industry standard 1, T/CAMDI065-2021 Additive manufacturing tantalum metal knee prosthesis, T/CAMDI 066-2021 Additive manufacturing tantalum metal individualized bone defect filler "and other group standards, and assisted in the completion of more than 500 cases of tantalum metal clinical application, implanted prostheses include tantalum metal intervertebral fusion bone spacers, hip joints, shoulder joints, knee joints, ankle joints, etc.
For more details, welcome to contact us
Article source: "China Device Review", edited by "Additive Remanufacturing Industry Research".