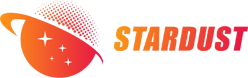
0 Preface
The rail/attitude control two-component liquid rocket engine is the power core of missiles, satellites, spacecraft and other space vehicles. In order to meet the demand of high specific impulse, lightweight, long life and high reliability of the engine, the material of the thrust chamber of the rail/attitude control engine is developing in the direction of ultra-high temperature and lightweight. Compared with molybdenum alloy and tantalum alloy, niobium-tungsten alloy has the advantages of low density, excellent high-temperature strength, and good plasticity, which is one of the most promising refractory metal materials [1]. Under the protection of molybdenum silicide high-temperature antioxidant coating, the working temperature of niobium-tungsten alloy thrust chamber can reach 1550℃. With the development of model development, the use of Nb521 niobium-tungsten alloy in China's aerospace field is more extensive, has been used in other high-speed vehicle components [2-3], Nb521 niobium-tungsten alloy high-temperature structural parts of the machining method has also been expanded to the spinning, welding and so on.
Niobium-tungsten alloy welding is prone to oxidation phenomenon leading to a sharp decline in material properties, the current research on the welding process of Nb521 niobium-tungsten alloy is relatively small, mainly focused on the electron beam welding. Zhu Dongmei and other scholars [4] carried out a Nb521 alloy electron beam welding process test research, the results show that Nb521 has good electron beam welding performance and excellent room temperature joint strength. Wang Feng and other scholars [5] found that Nb521 alloy and low-density niobium alloy has a better electron beam welding performance. Xia Mingxing and other scholars [6] successfully welded TC4 titanium alloy and Nb521 alloy by electron beam welding, and the weld organization is dense and defect-free. However, due to the limitation of the vacuum chamber size, the electron beam welding process will be difficult to meet the development needs of larger size niobium-tungsten alloy structural parts.
Laser welding is similar to the electron beam welding process, with high energy density, fast welding speed, small heat-affected zone, small deformation of the weldment, etc. [7], welding with the setup of oxidation protection devices, without vacuum chamber. Zhang Yanqiao and other scholars [8] carried out a thin-walled niobium alloy reinforcement and the matrix of the laser spot welding process research, alternative resistance spot welding to achieve the two high-strength connection. Laser welding as a welding method based on self-melting welding, smaller spot on the pre-welding workpiece assembly requirements are higher [9]. At present, little research has been reported on laser butt welding of niobium-tungsten alloy structural parts. Considering the future demand for welding of large-scale thin-walled Nb521 alloy structural parts and dissimilar thickness parts, the influence of assembly conditions (including assembly misalignment and assembly gap) on weld shaping, microstructure, and mechanical properties of the laser welded head of Nb521 alloy can be investigated through the welding tests, which can accumulate the basic data of Nb521 alloy laser welding and provide a good foundation for the development of Nb521 alloy laser welding. Basic data, for large thin-walled structural components of laser welding engineering applications to provide reference.
1 test method
Welding test plate selected thickness of 1.0mm and 1.5mm Nb521 alloy flat plate, Nb521 alloy main chemical composition is shown in Table 1. test plate specifications for 100mm × 60mm, bevel through the milling method of machining flat, the use of degreasing agent + pickling method to remove the surface oil and oxidized film, weld before the bevel will be wiped clean with alcohol.
The test is not open bevel laser butt welding form, as shown in Figure 1. 1.0mm + 1.5mm Nb521 flat plate bottom flush for the ideal assembly state, that is, defined as the assembly of the zero-error state, when the 1.0mm flat plate up the occurrence of the wrong side, the definition of the wrong side of the positive value; when the 1.0mm flat plate down the occurrence of the wrong side of the wrong side of the definition of the wrong side of the negative value.
Test to rated power 10KW fiber laser to achieve welding, laser beam incidence direction perpendicular to the surface of the welded test plate, focusing mirror focal length of 300mm, spot diameter of ϕ0.3mm. the rest of the welding process parameters are shown in Table 2, assembly gap of 0.3 ~ 0.5mm welded test plate to increase the amount of 2mm positive defocus.
After welding, cross-section metallographic samples and weld tensile samples were taken perpendicular to the direction of the weld and prepared respectively. LeicaDMI5000M metallographic microscope was used to observe the microstructure of the weld. The electronic universal tensile testing machine was used to test the room temperature tensile properties of the weld.
2 Test results and discussion
2.1 The effect of assembly misalignment on Nb521 alloy weld molding
1.0mm +1.5mm butt weld ideal assembly state for the back flush, taking into account the actual engineering production due to processing errors and other possible 1.0mm components upward misalignment or downward misalignment (Figure 2), so carry out different misalignment state in Figure 3 of the weld test, the study of the assembly of misalignment of the thickness of Nb521 alloy weld effect of dissimilarity. For 1.0mm +1.5mm Nb521 alloy butt weld, when the 1.0mm test plate 1.5mm test plate assembly for the zero-error state, front and back can be obtained uniform and beautiful weld formation; when the assembly of the amount of error for the +0.2mm to +0.3mm and -0.2mm, can still obtain uniform and beautiful weld formation, the effect of error state on the formation of the weld is not significant; when assembly When the amount of assembly wrong edge reaches -0.3mm, it can be seen that the weld forming is basically uniform, but the fullness of the front and back sides of the weld is reduced, and when the amount of assembly wrong edge reaches -0.5mm, the front and back sides of the weld forming deteriorates significantly, showing an unstable state.
The weld cross-section microstructure observation of the test plate assembled with 0mm , + 0.3mm , -0.3mm misalignment amount respectively, the results are shown in Fig. 4. Fig. 4d, Fig. 4e are the fusion zone and weld center microstructure in the state of 0mm misalignment, which is also the typical morphology of Nb521 alloy laser butt weld, and the rest of the misalignment state of weld morphology is basically the same as that of Fig. 4d and Fig. 4e. From Figure 4d and Figure 4e, it can be seen that the weld shows typical cast state organization, the columnar crystals near the fusion zone are based on the grains of the semi-molten base material, and grow relatively along the direction of maximum heat dissipation to the center of the weld by means of associative crystallization; the columnar crystals in the upper and lower regions of the center of the weld grow relatively on the two sides of the weld and under the tendency, respectively; the grains on the outer side of the fusion zone grow up by heat, and the width of the heat-affected zone is about The width of heat affected zone is about 0.3~0.4mm. From Fig. 4a, Fig. 4b and Fig. 4c, it can be seen that the weld presents consistent growth of columnar crystals under different misalignment states, i.e., the assembly misalignment has very little effect on the microstructure of the weld. When the amount of misalignment is 0mm, the frontal weld is tilted and smooth transition from the edge of 1.5mm test plate to 1.0mm test plate; the back weld is formed very full, with some raised back weld leakage; when the amount of misalignment is +0.3mm, the frontal weld is formed to be leveled due to the elevation of the 1.0mm test plate, and at the same time the back of weld is tilted in transition, with the weld leakage basically plane; when the amount of misalignment is -0.3mm, the frontal welding is formed in the same way as that of 1.0mm test plate, and the weld growth is very stable. When the amount of wrong edge is -0.3mm, the front and back of the weld show obvious depression, and the cross-sectional morphology of the weld coincides with that of the front and back of the weld in Fig. 3.
Misalignment amount of - 0. 2 ~ + 0.3 mm of the test plate weld forming and cross-sectional morphology and 0mm misalignment amount of test plate differences are small, so the amount of misalignment of 0mm, - 0.3mm test plate room temperature tensile properties test, the results are shown in Table 3. Table 3 shows that the assembly of misalignment of 0mm and - 0.3 mm state, all the fracture of the specimen is located far away from the weld of the 1.0 mm base material, the joint Strength indicators did not see a significant difference; fracture and tensile direction of 45 °, and accompanied by obvious necking phenomenon, for the typical toughness fracture characteristics, that is, when the 1.0 mm test plate down the staggered edge in +0.3 mm or less, the Nb521 alloy weld is still maintaining good overall mechanical properties. In addition, the extreme difference in tensile strength of each group of specimens for 10 ~ 12MPa, because the specimens are fractured in 1.0mm base material, and the base material Nb521 alloy sheet processed through the cold-rolling process, it is inferred that tensile properties of the raw material for the normal performance fluctuations in the error.
2.2 The effect of assembly gap on Nb521 alloy weld molding
In order to study the effect of assembly gap on dissimilar thickness Nb521 alloy laser weld, 1.0mm +1.5mm Nb521 alloy butt weld preset gap test, different assembly gap state weld molding as shown in Figure 5. As can be seen in Figure 5, when the 1.0mm test plate and 1.5mm test plate assembly gap of 0mm state, the front and back can be obtained uniform and beautiful weld forming; when the 2 test plate preset gap increased to 0.3mm, can still obtain uniform and beautiful weld forming, gap state on the weld does not have a significant impact; when the preset gap increased to 0.5mm, the weld can not be formed normally, the 2 test plate did not form a Connection.
Metallographic observation and mechanical property testing of weld cross-section were carried out on test plates with different presetting gaps, and the results are shown in Fig. 6 and Table 4. As can be seen from Figure 6, under the preset 0.3mm assembly gap condition, the Nb521 alloy laser butt weld also shows the same columnar crystal growth morphology consistent with the zero-gap condition, and the front and back sides of the weld are shaped basically flush, with no significant concavity. The weld tensile specimen also fractured in the 1.0mm base metal away from the weld, a typical toughness fracture characteristics. Joint strength index has a small reduction in the normal fluctuations in the performance of the base material. That is, when the 1.0mm test plate and 1.5mm test plate assembly gap does not exceed 0.3mm, the weld can still get good positive and negative molding and comprehensive mechanical properties.
3 Conclusion
(1) 1.0mm +1.5mm Nb521 alloy laser butt weld allows the maximum assembly misalignment of 0.3mm, the maximum assembly gap of 0.3mm, that is, no more than the thickness of the base material (calculated as a thin plate) of 30%.
(2) Nb521 alloy has a good laser welding process, the weld metallographic organization is typical of the cast state organization, the two sides of the columnar crystals through the association of crystallization to the weld center of the relative growth of the heat-affected zone width of about 0.3 ~ 0.4mm; assembly misalignment and assembly gap on the weld microstructure of the influence of small.
(3) Assembly misalignment and assembly gap does not exceed the maximum value allowed, can obtain uniform and beautiful positive and negative weld shaping; joints with good comprehensive mechanical properties, tensile specimen fracture in the base material, a typical toughness fracture characteristics.
reference: (C)1994-2023 China Academic Journal Electronic Publishing House.All rights reserved. http://www.cnki.net
The spherical Nb521 alloy powder prepared by Stardust using RF plasma spheronization process has high purity (oxygen content ≤ 500ppm), high sphericity (sphericity > 95%) and uniform particle size distribution (0-150μm optional), which effectively improves the powder fluidity and molding densities. The non-contact high-temperature purification process significantly reduces the residual impurities, resulting in powders with excellent high-temperature stability, corrosion resistance and mechanical strength, which are suitable for aerospace high-temperature components, irradiation-resistant components for the nuclear industry, 3D printing of complex structural components and other high-end manufacturing fields. The products strictly follow the industrialized standards, taking into account the performance and consistency, more technical details and application cases can be contacted Stardust Technology Manager Cathie Zheng +86 13318326187 to get.