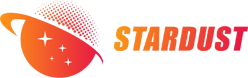
1 Preface
Nb521 niobium-tungsten alloy belongs to the ultra-high temperature materials, also known as refractory materials, has excellent high-temperature mechanical properties and excellent process performance, the maximum operating temperature of 1900 ℃, to meet the engine on the use of ultra-high-temperature material performance requirements, a substantial reduction in the flow of propellant used to cool the combustion chamber, which is conducive to improving the performance of the engine [1]. With the increase in demand for the development of new models, Nb521 niobium-tungsten alloy in China's aerospace field is more widely used, not only in the missile engine used in other high-speed vehicles, some high-temperature parts are also beginning to use. Such as a new missile engine combustion chamber tail nozzle part, the operating temperature up to 1600 ~ 1800 ℃, to be selected Nb521 material manufacturing fasteners, connecting the part of the composite material. In this paper, through the Nb521 material fastener manufacturing process research, in order to find a suitable processing technology, so as to meet the new type of task requirements.
2 material properties
2.1 Chemical composition characteristics
Nb521 niobium-tungsten alloy density of 8.65 ~ 9.0g/cm3, the chemical composition of its matrix for the Nb, pure metal Nb W, Mo, Zr and other elements have a high degree of solid solubility, these elements and Nb form a variety of solid solution strengthening phase, can significantly enhance the alloy's room and high-temperature mechanical properties; W and Mo two elements of the melting point is high, the atomic radius of the elements with Nb is similar to increase the high-temperature Nb alloy W and Mo two elements with high melting point, atomic radius similar to the Nb element, can improve the high temperature strength and creep properties of Nb alloy; Zr mainly play a role in the formation of reinforced phase, enhance the strength of the Nb matrix [2].The common chemical composition of Nb521 material is shown in Table 1.
2.2 Mechanical properties and microstructure characteristics
From the chemical composition of Nb521, it can be seen that it mainly contains Nb and W two elements. With the increase of W content, the melting point of Nb alloy gradually increased, Nb and W form a body-centered cubic structure (bcc) solid solution, can not be strengthened by heat treatment aging.Nb521 bar delivery state for recrystallization annealing, microstructure for the fine equiaxial organization (see Figure 1).
Figure 1 Microstructure of annealed state
Nb521 bar room temperature mechanical properties are shown in table 2. room temperature, the material has low tensile strength, plasticity and toughness, has good plasticity, can be formed by forging, upsetting and other plastic processing methods.
The C element in Nb521 alloy forms various types of carbides such as MC, M2C and M3C2 with W, Mo and Zr, which are diffusely distributed in the alloy matrix and play the role of pinning grain boundaries and dislocations, which is a more effective high-temperature strengthening method [3]. However, with the increase in heating temperature, the strengthening phase began to precipitate and aggregate growth, resulting in a decline in the high-temperature strength of the alloy [4].Nb521 bar high-temperature mechanical properties are shown in Table 3, it can be seen that the material at 1600 ℃ still has good tensile properties (Rm ≥ 70MPa), to meet the engine thrust chamber 1600 ℃ when the material's tensile strength ≥ 60MPa requirements, it can be seen that Nb521 material fully meets the requirements of the engine thrust chamber.
3 Material Forming Properties
3.1 Forming properties of upsetting
Nb521 material in solid solution state has good ductility and deformability, upsetting ratio (rod material upsetting part of the original length and diameter of the ratio) up to 2.3 or more, in the manufacture of fasteners can be used in the process of upsetting into shape. Upsetting into shape can not only save materials, reduce costs, but also can control the head of the combined part of the metal flow, improve the fatigue life of the product.
When processing hexagonal head bolts with Nb521 material, 3 kinds of problems should be solved in the process of cold upsetting: ① Raw material billet size problem. ② Raw material surface lubrication problems. ③ Cold heading mold design problems. As for the size of raw material blank, it is mainly through the calculation of bolt head material and its deformation ratio, so that the size of the screw blank before rolling the thread can get an optimal value. The surface lubrication of raw material, because Nb521 material and cold heading mold working surface adhesion than heat-resistant steel and stainless steel is much stronger, so in the cold heading forming before, must be lubricated for cold heading blanks, eliminating the phenomenon of sticking to the mold, and improve the life of the upsetting mold. Through verification and comparison, the lubrication program of coating molybdenum disulfide on the surface of the blank before cold heading was selected, which effectively solved the problem of sticking die of cold heading blanks. In terms of mold design, the blank deformation process of hexagonal head bolts in double-strike cold heading machine is shaped by upsetting cylindrical head (i.e. pre-punching and final upsetting) in two steps (see Fig. 2). This method is mainly to reasonably design the pre-punching die, after adjusting and trial upsetting to correct the shape after the initial upsetting, curing the die, and realizing the upsetting of this kind of products in small batch production.
Fig. 2 Cold heading molding
1-Cutting knife 2-Block 3-Cutting die 4-Pre-punching die 5-Rod die 6-Final heading die 7-Ejector rod
3.2 Mechanical processing performance
Nb521 high-temperature fasteners are subject to extremely harsh service environment, which requires high surface quality, and the surface machining traces and integrity have an important impact on the service quality. Due to the existence of poor cooling performance, tool shank vibration and not easy to chip removal and other processing difficulties [5], in the turning and grinding process, there is a phenomenon of easy wear of the tool, the product has obvious turning lines, poor surface quality, so it is necessary to use CNC lathes and centerless grinders, etc., to carry out precision machining of the fastener rod. The processing efficiency of fasteners can be effectively improved by selecting suitable tools and formulating the most suitable processing parameters.
(1) Select the appropriate tool and grinding wheel material because of the low hardness of the material, so in the turning and grinding process, you can choose a faster processing speed and a larger amount of turning, to ensure that the surface roughness and dimensional consistency of the product. However, attention should be paid to cooling during processing to avoid grinding burns. CNC lathe DNMG110408MS, VNMG160404N and other different tools, adjust the relevant speed and feed, can ensure the size and appearance of the CNC turning process requirements. At present, the grinding wheel material commonly used in fastener grinding is silicon carbide and white corundum, through the process verification, the selection of silicon carbide material grinding wheel for grinding processing, centerless grinding machine processing efficiency can be greatly improved, and can better ensure the appearance quality and size requirements of Nb521 fasteners.
(2) Determine a reasonable grinding allowance thread using cold roll forming method, the diameter of the screw blank needs to be ground. In the process of grinding the screw blank rod, CNC lathe reserved grinding margin is appropriate, for grinding processing product qualification rate and processing efficiency has an important impact. If the use of silicon carbide material grinding wheel, according to conventional parameters, only 0.03mm grinding on one side for grinding, there will be uneven product size, local point of super poor and surface roughness is difficult to ensure that the size can not be guaranteed, can not be batch processing. After many times of verification, under the premise of ensuring product quality, choose the most reasonable machining allowance of 0.10mm, and adopt the processing mode of rough grinding + fine grinding, which can effectively ensure product quality and improve the efficiency of grinding processing.
3.3 Roll forming technology for external threads
Since the thread is a typical feature of fasteners, its forming quality greatly affects the structural strength and performance level of fastener products, therefore, most of the high-performance fasteners in aerospace and other fields use rolling to process the thread. Rolling threads refers to the precision rolling machine tool on the metal billet radial extrusion, so that the metal produces plastic deformation and the formation of threads, and make the threads to strengthen the processing technology. Compared with turning threads, rolling threads are characterized by high material utilization, good surface quality, high thread strength and surface hardness as well as high fatigue life and production efficiency. Thread in the rolling forming process, the plastic deformation resistance of the material increases, hardness and strength is improved, while plasticity and toughness decline, that is, the phenomenon of work-hardening, very easy to make the top of the threaded teeth to form cracks and folding and other defects. For this kind of difficult-to-machine material thread processing technology, through the thread forming process analysis, calculation and verification of rolling thread thread thread thread blank diameter, determine the rolling pressure, roller speed, roller feed speed and cutting fluid selection and other major process elements, to solve the cold rolling processing of rolling wheel chipped teeth and fasteners thread folding exceeded the standard and other issues, to ensure that the rolling thread after the external surface quality of the thread. The bolt metal flow line is shown in Figure 3.
3.4 Internal thread tapping thread forming difficulties and solution measures
Nb521 alloy material has good plasticity, but cutting processing is difficult, there is a clear tendency of chip abrasion or bonding. if Nb521 material nut is processed by ordinary cutting taps, due to the viscosity of the material, the chips are in the form of bands during processing, which are easy to be abraded or stick to the cutting edge, resulting in an increase in the cutting force and an increase in the cutting temperature, and at the same time, it is easy to produce a tear phenomenon on the surface of the workpiece, and defects such as rotten teeth, tooth side wrinkles and incomplete tooth shape will occur in the process of threading. Rotten teeth, tooth side folds and tooth type incomplete and other defects, so in order to ensure the normal processing of the product, according to the characteristics and requirements of the cutting process of Nb521 material, you need to choose the right tap and reasonable cutting dosage. So the development of niobium tungsten alloy materials special cutting taps and extrusion taps, by adjusting the size of the bottom hole and other measures, the processing of the thread side surface roughness value of Ra up to 1.6 μm, thread through the stop gauge test qualified to solve the problem of sharp edges of the thread tip and burr, reducing the difficulty of tapping thread processing, thread did not appear rotten teeth, tooth side folds and incomplete defects such as tooth shape, the quality of the thread to meet the standard requirements.
4 Fastener performance indicators
Nb521 material manufactured bolts, screws, studs and nuts and other types of fasteners, product structure with reference to the HB series of standards. In order to verify the Nb521 fastener standard performance indicators and measured conditions, to determine the stability and reasonableness of the performance of Nb521 material, in accordance with the aerospace model of the most commonly used types of head, type and typical specifications of the selection of bolts, screws and nuts to verify its performance, its strength and hardness testing. The measured properties of Nb521 products are shown in Table 4.
5 Surface treatment
At present, the main way to improve the refractory metal in the high temperature oxygen environment to resist high-temperature oxidation ability of alloying and surface coating two ways. The alloying method can improve the antioxidant properties of the alloy, but the alloying elements must exceed a certain amount of critical value will play a protective role in the matrix, which will inevitably affect the other properties of the alloy, in particular, will result in a decline in the mechanical properties of the matrix at high temperatures. And in the alloy surface plus system coating, both to protect the alloy matrix from high temperature corrosion or slow down the corrosion rate, and will not change the composition of the alloy matrix, the alloy can be retained to the maximum extent of high temperature mechanical properties.
Nb521 manufactured bolts, screws, studs and nuts fasteners used in the surface treatment method for the surface of the addition of the coating, prepared by slurry melting and burning method, for the excellent performance of the silicide composite coating [6], the thickness of the coating (60 ± 10) μm. coating detection and high temperature performance to meet the atmospheric environment: 1600 ℃ static antioxidant life requirements ≥ 1h; 1800 ℃ static antioxidant life requirements ≥ 0.5h; 1800 ℃ static antioxidant life requirements ≥ 0.5h; high temperature properties to meet the atmospheric environment: static antioxidant life requirements ≥ 1h. Requirements ≥ 0.5h; 1800 ℃ cooling (water cooling) to room temperature, thermal vibration life ≥ 50 times.
6 Conclusion
This paper comprehensively analyzes the characteristics of Nb521 material, upsetting into shape performance, machining performance and fastener structure characteristics, and formulates the comprehensive performance index of Nb521 material fasteners. Through innovation and optimization of traditional processing technology, the application of new molybdenum silicide coating and other measures to solve a series of difficult problems in the manufacture of Nb521 fasteners, the production of fasteners to meet the design and specification requirements, has been successfully applied to a new type of equipment engine combustion chamber tail nozzle parts, connecting the parts of the composite material, the operating temperature of 1600 ~ 1800 ℃. The results show that: Nb521 niobium-tungsten alloy has excellent process performance and high-temperature performance, can meet the use of aerospace fasteners on the material performance requirements.
reference:(c)1994-2023chinaAcademicJournalElectronicpubolishingHouse.Alrightsreserved.http://www.cnki.net
Stardust's spherical Nb521 alloy powder is prepared by plasma spheronization technology with high purity and high sphericity, suitable for 3D printing and powder metallurgy, and widely used in aerospace, medical devices and energy fields. Its main features:
- High temperature stability: it remains stable in high temperature environment and possesses antioxidant performance, which is suitable for manufacturing high temperature parts.
- High sphericity and flowability: Spherical structure brings good flowability and filling density, which contributes to molding quality in additive manufacturing.
- Low Oxygen Content: Controlled oxygen content to ensure purity, suitable for demanding manufacturing environments.
- Biocompatibility: Suitable for the manufacturing of medical implants.
Stardust's Nb521 alloy powders provide consistency and flexibility in the manufacture of high performance, complex parts.
If you are interest in spherical metal powder.Please feel free to contact our manager Cathie Zheng.+ 86 133 183 26 187