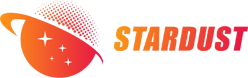
Abstract: The oxidation behaviors of tantalum-tungsten alloy with 10-20% W was investigated between temperature range of 700 to 900 ℃ exposed in air. The kinetics of Ta-W alloy was determined by TG-DTA, the characteristics of oxides were analyzed by SEM, EDS and XRD. The oxidation tests revealed that the alloys obeyed parabolic kinetic in the initial stage, then translated in linear law. The addition of W has a good effect on the oxidation resistance of Ta-W alloys at experimental temperature. Solid solution of Ta2O5 form in case of oxidation product of Ta-10W, Ta-15W alloys, while the complex oxide Ta22W4O67 form after Ta-20W alloy oxidized. The formation of solid solution and complex oxide impeded the volatilization. The compact oxide film protects the penetration of oxygen in the initial oxidation stage. The large compressive stresses and mismatch of the coefficient of thermal expansion between oxide scale and matrix alloys make the oxides layer be broken, which cause kinetic of oxidization obeying linear law.
Introduction
Tantalum(Ta) and tungsten(W) have very high melting point, good erosion resistance, high strength and elastic modulus. The Ta-W alloys show a combination of properties not found in many high temperature metals. Due to these unique features, Ta-W alloys have been considered as candidate for structural materials for aero-engine applications [1-3]. But the applications at high temperature are restricted due to the poor oxidation resistance of the alloys [4].It has been reported that tantalum exhibits a complex oxidation behavior. The oxidation reaction included oxygen dissolution in metal and formation of sub-oxides and higher oxides. When tantalum oxidized between 450 to 600 ℃, the parabolic kinetics were found and the oxidation involved an oxygen dissolution in metal followed by formation the metallic oxide phase TaOy and TaOz [5,6]. The parabolic stage indicated that the oxygen dissolution into Ta-O solid solution [7]. The activation energy was calculated as 121 J/mol, which corresponded to the activation energy of oxygen diffusion into the Ta-O solid solution. Oxidation of Ta in 600 ℃exhibits a parabolic behaviors initially due to form oxide film, then after about 20 min linear rate law is observed [8]. Li used acoustic emission method to measure critical stress of Ta oxide film and found that after 24 min exposed in air at 600 ℃, the film broken, then after 34min spalling from the matrix [9]. According to Stringer, from 600-800 ℃, TaOZ sub-oxide formed a porous L-Ta2O5 film with numerous voids due to the different densities of Tantalum, TaOz, and Ta2O5. Oxidation of pure Ta is controlled by the processes at the metal-scale interface [10]. Above 600 ℃, the transition from parabolic to linear is observed, which means the cracks continuously formation in Ta2O5metal-oxide film and leading to break. At high temperature, [11] the transition from parabolic to linear is due to the formation of Ta2O5, which cracks continuously as it is formed leading to breakaway. The parabolic stage length decreases with increasing temperature: from a duration of 400-800 min at 450 ℃ to complete disappearance at 600 ℃. At 800 ℃ the mechanism changes and the oxide produced is not anymore TaOz but more likely traces of sub-oxides and TaO. This disastrous oxidation behavior is referred as “pesting” oxidation [12].The research of oxidation behavior of tungsten showed that between 350 to 600 ℃, tungsten oxidized in a very slow speed with parabolic kinetics. When temperature increased to 500-1000 ℃, the oxidation speed increased quickly, and the initial stage parabolic kinetics were found, then changed to be linear. At higher temperature, the oxidation reaction is gas transport controlled [13, 14]. Above 700 °C, WO3 forms a yellow powdery outer layer of high porosity on oxidized tungsten. Underneath the porous trioxide layer there is a dense, thin, dark blue, adherent layer of uncertain composition, probably some intermediate oxide of tungsten [15]. Anna Warren studied the bulk polycrystalline tungsten oxidized at room temperature to 500 ℃ with ESCA-analysis. The results
showed that unlike the tantalum form TaOz or lower valence sub-oxides at lower temperature, the formation of WO3, regardless of the oxidation temperature was observed. The oxide form relative thin with oxidation temperature is lower than 200 ℃, the oxide thickness increases markedly with temperature is up to 400 ℃ [16].Although some studies had been done for oxidation behaviors of pure tantalum and tungsten metals, there is still lack of knowledge for oxidation behaviors of tantalum-tungsten alloy. Only few researches reported the oxidation behaviors of low W content alloy such as ASTAR-811C (Ta-8 wt.% W-1 wt.% Re-0.7 wt.% Hf-0.025 wt.% C ) [17] and T111 (Ta-8wt % 2wt% Hf) [18]. In this work the oxidation of tantalum-tungsten alloy with higher W content (10-20%) was investigated between 700 to 900 ℃ exposed in air. The oxidation kinetics and mechanism of alloy were studied in some detail.
Experimental
The raw materials used in the present study were Ta, and binary alloy Ta-10W, Ta-15W and Ta-20W (weight percent) which were processed by electric beam melting under high vacuum. The chemical composition of samples is given in Table1. Samples were cut by wire electro-discharge machining for micro-structural examination and oxidation studies.The samples for oxidation testing were cutting to about 3×4×1mm and polished by 600 mushes. Small specimens having mass less than 300 mg were subjected to simultaneous thermogravimetry (TG) and differential thermal analysis (DTA) on a TG-DTA machine (Netzschsta 449 F3 Jupiter, Germany) to study the oxidation behavior. The nonisothermal experiments were carried out in air at the temperature range of room temperature to 900 ℃, with heating rates 10K /min, using a Pt crucible and the inert Al2O3 powder as reference. The isothermal oxidation behaviors were tested at the temperatures of 700 ℃, 800 ℃ and 900 ℃. The oxidized specimens were examined using X-ray diffraction (XRD) on Simazu X-6000 to identify the phases present. The microstructures and elements analysis of the alloys oxidation were examined with scanning electron microscope (JSM-6301) equipped with energy diffraction scope (EDS). For identified crystal structure of the oxides, the complete oxidation samples were prepared by oxidation alloy at 1200 ℃ for 6 h.
Results
Nonisothermal Oxidation. Non-isothermal oxidation behaviors of both pure Ta and Ta-W alloys samples have been studied by using TG analysis through recording of the variation of mass change with the temperature up to 900 ℃ (heating rate of 10K/minute), and the results are depicted in Fig.1. On examination of the presented TG data, it is revealed that the temperature for initiation of mass change in the pure Ta (about 600 ℃) is lower than those for the Ta-W alloy samples (about 680 ℃). This difference can be explained by considering the fact that the pure Ta is more prone to oxidation than alloy samples. The total mass gain as a fraction of the initial mass due to the oxidation is the highest in pure Ta, followed by that of Ta-15W, Ta-20W, Ta-10W alloy.
Isothermal Oxidation. Fig. 2 shows the plots displaying the oxidation kinetics of alloys at 700 ℃,at the start of oxidation the parabolic kinetics were found of Ta-W alloys, while at some time, linear behaviors were observed in pure Ta. The transition times of parabolic to linear oxidation of Ta-W alloys were 22.5 min, for Ta-10W, about 24 min for Ta-15W, Ta-20W alloy respectively. The weight gain per unit area as the function of oxidation time of alloys at 800 ℃ are shown in Fig. 3. The transition times of parabolic to linear oxidation of Ta-W alloy were shorten to 16 min, 19 min, 24 min for Ta-10W, Ta-15W, Ta-20W respectively. Ta-10W alloy show slightly better oxidation resistance at the temperatures of 700 ℃ and 800 ℃.
The Oxidation behavior of Ta-W alloy at 900 ℃ was different with those in 700-800 ℃. The oxidation kinetic curve of alloys at 900 ℃ is shown in Fig. 4. Ta-15W and Ta-20W alloy showed parabolic trend other than linear trend. V. B. Voitovich pointed out that at 900-1000 ℃, the tantalum samples showed increasing oxidation resistance and longer parabolic –stage duration. This character is related to the L- Ta2O5 defected structure [6]. Ta-10W showed higher mass gain per unit than other alloys, although less than pure Ta.
Oxides Characterization. The surface morphology of Ta-W alloys oxidized at 800 ℃ for 0.5 hr is shown in Fig. 5. The characteristic of the scale formed by oxidized were similar no matter of the W content. Rough and prone surface to spallation can be observed after oxidized for 2 hours. The cross section of Ta-10W oxidized for 0.5 h at 800 ℃ is present in Fig. 6, a relative dense oxidized layer without porous was observed. The oxidation product contained both tantalum and tungsten, at depths of the oxidation product the concentrations of tantalum, tungsten, and oxygen remained essentially constant. Elements analysis by EDS showed that the concentration of elements in oxides layer in weight present of Ta:W:O=76:8:16, or in atom ratio of Ta:W:O =29:3:68. The XRD patterns for oxide layer showed that no tungsten oxides were identified, while, the peak shift of Ta2O5 indicated the solid solution of WO3 to Ta2O5. After oxidized time increased to one hour, an oxide layer spall from the matrix with a thickness of 50 μm and in the surface of matrix (Fig. 7), and similar gray layer with thickness of about 15μm was observed. The element analysis indicated the spall layer had similar elements content with the oxide layer for 0.5 hour. While, at the oxidized layer in the surface of matrix, the concentration of Ta increased with the depth, and oxygen concentration decreased, that corresponds to the thickness of the oxidation product. As the oxidized time increased to 2 hour and 4 hours (see in Fig. 9), the spall layer broken into pieces while the similar thickness oxides layer still remained.
The cross section of Ta-20W after oxide 1 hour is shown in Fig. 10. It can be observed that the elements analysis results was different with Ta-10W. The spall oxidation layer was about 40 μm thickness and the atom ration of Ta:W:O was 4:1:8, the XRD pattern showed that a complex oxide Ta22W4O67 formed at spall (Fig. 11). The EDS analysis of the oxidized layer on the surface of alloy showed that the essential constant of Ta,W,O kept in 15μm thickness, while O concentration decreased with Ta, W concentration increasing with the depth of about 10 μm.
Discussion
The oxidation mechanism of Ta-W alloys is discussed according to the experimental results above: first, adsorption of oxygen by the surface, then reaction or incorporation of adsorbed oxygen atoms, and diffusion of oxygen into the alloy. Since activation free energy of tantalum is lower than that of tungsten, tantalum is the primary reaction in the oxygen other than tungsten oxidized. At experimental temperature, the highest valance oxides are formed. In this experiment, No porous L-Ta2O5 or WO3 were observed. The reason was that the WO3 formed from solid solution in Ta2O5 instead of volatilization. The solid solution has pseudo-hexagonal orthorhombic structure with sub-cell a=6.20A, c=3.89A with different b. High valence W6+ ionic incorporation into lattice of Ta2O5, decreased the concentration of inter ionic [19]. In case of Ta-20W alloy, due to high content of tungsten oxide, solid solution reached to solution limit then leading to the formation of Ta22W4O67 [20]. The formed compact solid solution oxidized layer impeded the volatilization of tungsten oxide. The dense oxide layer can provide protection to delay the penetration of oxygen. In this case, the initial oxidation kinetics obeyed parabola law, indicates that the rate of oxidation was controlled by a solid-state diffusion process. In order to perform well as a stable and protective 304 Functional and Functionally Structured Materials IV oxide layer, the oxide scale should present high density and good adhesion to the underlying metal. Although the oxide layer of Ta-W alloys is compact, the presence of lateral stresses, which may be attributed to the epitaxial misfit between the oxide and the underlying metal, can turn the oxide in a non-protective scale. For tantalum oxide and tungsten films the Pilling-Bedworth ratios are 2.33 and 3.4 respectively, one of the highest [21], thus developing large compressive stresses in the oxide scale. These stresses cause the cracks or fracture of the oxide, which loses its protective function. Mismatch of the coefficient of thermal expansion between oxide layer and matrix cause oxide scale separate from the matrix, and make oxygen easily through oxidation layer surface, the oxidation kinetics law translated to linear law. Oxygen uptake was controlled by the adsorption rate (or rate of arrival) at the gas-metal interface and the rate was linear with time rather than parabolic, which was usually associated with a diffusion-controlled mechanism.
Conclussion
The oxidation of tantalum-tungsten alloys with high tungsten content (10-20% W) are investigated under the exposed temperatures between 700 to 900℃ in air. Comparing with pure tantalum, Ta-W alloys show less mass gain under all the oxidation temperatures. The addition of W has a good effect on the oxidation resistance. The formation of solid solution of Ta2O5 and complex oxide Ta22W4O67 imped the volatilization of tungsten oxide, and therefore in the initial stage of oxidization the parabolic kinetic has been observed. The large compressive stresses and mismatch of the coefficient of thermal expansion between oxide scale and matrix alloys make the oxides layer be broken, then the kinetic of oxidization obeys linear law.
About Stardust Technology
Stardust Technology (Guangdong) Co., Ltd. is a national high-tech enterprise specializing in the research, development, production and sales of high-end spherical powder materials for 3D printing, powder metallurgy, surface engineering and other fields. The company insists on taking radio frequency plasma spheroidization powder making technology as the core and provides internationally advanced powder products and application solutions.
The company's main products include high-end rare refractory metals such as tungsten, molybdenum, tantalum, niobium, vanadium, rhenium, chromium and their alloys, compound spherical powders. At the same time, it provides technical services such as radio frequency plasma spheroidization, plasma rotating electrode atomization, 3D printing, hot isostatic pressing, injection molding, powder metallurgy, etc.
The spherical Ta-W refractory alloy powder produced by Stardust Company is made by radio frequency plasma spheroidization and atomization method. It has high purity and oxygen deficiency, high sphericity, smooth surface, no satellites, uniform particle size distribution, excellent flow performance, loose density and vibration density. Advanced features.
Tantalum-tungsten alloy is a high-density material with high melting point, high tensile strength, good dynamic ductility and corrosion resistance. It has far-reaching influence in the fields of chemical anti-corrosion, machinery, aerospace and military industry.https://zh-cn.stardustpowder.com/spherical-refractory-ta-55w-alloy-powder53-150mm
For More info,welcome to contact
Paper citation information:
Materials Science Forum Submitted: 2019-07-26
ISSN: 1662-9752, Vol. 993, pp 299-306 Revised: 2019-08-27
doi:10.4028/www.scientific.net/MSF.993.299 Accepted: 2019-10-08
© 2020 Trans Tech Publications Ltd, Switzerland Online: 2020-05-22