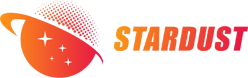
Ta-W alloy has high high temperature strength, good ductility, weldability and excellent corrosion resistance. It is suitable for working environments such as high temperature, high pressure and corrosion resistance. It is widely used in chemical industry, aerospace, atomic energy industry and high temperature technology. It is a very important engineering and functional material.
Ta10W alloy is an important member of the Ta-W alloy family. Its corrosion resistance is similar to that of tantalum. It has good stability in acidic and neutral media and can withstand high temperature and mineral acid (hydrochloric acid, nitric acid and sulfuric acid) corrosion better than other materials. At the same time, it has excellent thermal conductivity, which is more than twice that of titanium, more than three times that of zirconium and stainless steel, and four times that of nickel-based alloys. It is an ideal material for manufacturing chemical reaction vessels, heat exchangers and heat transfer components such as condensers, bayonet heaters, spiral coils, U-tubes, sprayers and reboilers.
Ta10W alloy has a density of 16.78~16.90g/cm3 and a melting point of 3080℃. It has very good room temperature and high temperature mechanical properties. At a high temperature of 2000℃, its tensile strength can still reach 100MPa, and it also has very good welding performance. Ta10W alloy has high high temperature strength, but its elongation does not exceed 50%. It has good high temperature creep resistance and excellent high temperature durability. Its excellent performance makes Ta10w alloy very important in the aerospace field.
Ta10w alloy has high chemical stability to liquid metal mercury, sodium, and sodium-potassium alloy. It is mainly used in the atomic energy industry to manufacture liquid metal containers and diffusion walls of high temperature heat release elements. In the field of space applications, it is mainly used for the outer sheath of isotope reactors (working temperature is about 600℃), as well as heaters (2000~2200℃) or high temperature chucks used in satellites or probe vacuum. In the field of weapons and equipment, Ta10w has been successfully applied to high-temperature resistant parts in the gun bore. The locking device of the rocket launcher (gas temperature 3300℃, solid temperature 1800~1900℃, launch time 0.6~0.8s) uses Ta10w powder coating on its surface, and the bullet-blocking lever support, ignition contact and directional tube plug-in mechanism all use Ta10W alloy.
High-temperature alloys generally require two performance requirements at the same time, namely excellent high-temperature mechanical properties and high-temperature corrosion resistance. However, the two aspects of the performance of the same alloy are sometimes contradictory and cannot be optimized at the same time. Ta10W alloy has excellent high-temperature mechanical properties, but its high-temperature oxidation resistance in the atmosphere is relatively poor. At 300℃, Ta10W alloy will oxidize. The higher the temperature, the more intense the oxidation, until it is completely "powdered" and destroyed. This shortcoming limits the application scope of Ta10W alloy.
At present, the main ways to improve the high-temperature oxidation resistance of tantalum-tungsten alloys in the atmosphere are alloying protection and surface coating protection. The alloying method can improve the oxidation resistance of the alloy, but the alloying elements must exceed a certain critical value to protect the matrix. This will inevitably affect other properties of the alloy, especially causing the decline of the high-temperature mechanical properties of the matrix. It can be seen that the alloying method has its own limitations. After the coating is added to the surface of the alloy, the coating can protect the alloy matrix from high-temperature corrosion or slow down the corrosion rate without changing the composition of the alloy matrix, and can retain the high-temperature mechanical properties of the alloy to the greatest extent.
1 Research process
1.1 Selection of coating system
Common high-temperature oxidation-resistant coatings for tantalum-tungsten alloys include heat-resistant alloy coatings, aluminide coatings, silicide coatings, and precious metal coatings. The silicide coating is used for the high-temperature oxidation-resistant coating of Ta10W alloy this time because the silicide coating has good thermal stability and can be used at a temperature of up to 1600℃. The SiO2 on the surface of the coating can effectively prevent oxygen from diffusing into the matrix; and SiO2 is fluid at high temperatures, so the coating has a certain self-healing ability and can withstand certain deformation.
1.2 Coating principle
Based on the complementary properties of metals and non-metals, powder materials with certain solid solution and bonding properties can be used to react the components in the powder with the alloy surface through melting, sintering and other methods to form a dense layer of intermetallic compounds, which wraps the alloy inside and slows down or even prevents the invasion of oxygen in a high temperature environment, thereby improving the oxidation resistance of the alloy material. The coating is mainly composed of three layers: the first barrier layer, usually an oxide, blocks the invasion of external oxygen; the second barrier layer is the main body of the coating. At high temperatures, the coating body has a dual role. Its outer surface part supplements the volatilized elements of the oxide layer, gradually forming the volatilization of the oxide layer, and the inner surface layer blocks the element transition of the third layer, and compensates and reinforces the diffusion layer; the third layer is the diffusion layer, which is mainly to make the mutual corrosion between the alloy and the coating in a dynamic equilibrium state.
1.3 Coating preparation
1.3.1 Selection of coating raw materials
The main material of the coating is Si-Cr-Ti mixed powder. On this basis, a certain amount of metal element powder is added as a coating activator to improve the bonding strength between the coating and the alloy substrate and improve the coating performance. The main activators and their functions are shown in Table 1.
1.3.2 Coating coating method
Use element powder with a purity of 99.7% and above 250 mesh, mix evenly in a certain proportion, use ethanol as a solvent, stir and grind thoroughly until the sintering requirements are met. The coating method adopts the dip coating method. After the slurry is prepared, the alloy test piece is completely immersed in the slurry, and then taken out at a uniform speed after 1 to 2 seconds. After the test piece is dried, a uniform coating layer can be obtained on the alloy surface. Then use a vacuum resistance furnace to heat to the design temperature and keep it warm.
1.3.3 Selection of coating sintering process parameters
Since the melting point of Ta10W is as high as 3080℃, in order to form a coating on the alloy surface through solid solution and diffusion, in addition to the solid solution and semi-solid solution characteristics of the coating powder, a higher coating sintering temperature needs to be selected. After many studies, the coating sintering temperature is finally established as: 1500℃~1600℃, and the insulation time is 10~30min.
2 Organization and Properties
2.1 Coating Metallographic Analysis
It can be seen from the above figure that the Ta10w coating has a clear hierarchical structure, with obvious barrier layer and diffusion layer structure, and a tight structure without obvious defects such as pores. This plays an important role in reducing the oxygen penetration pathway in the coating, slowing down the oxidation rate of the alloy, and slowing down the volatilization of alloy elements, and can significantly improve the high-temperature oxidation resistance of the alloy.
2.2 Coating performance
The coating performance is measured by the internal heat method, and the static oxidation resistance and thermal shock resistance of the coating are measured respectively. The temperature of the test piece is measured by an infrared thermometer. When measuring the static oxidation resistance of the coating, the test piece is clamped in the middle of the two electrodes, and the power is turned on to heat it to the required temperature. The temperature of the test piece is controlled by adjusting the current and voltage. When the test piece has small black spots visible to the eye, it indicates that the coating has defects. The performance test time is the coating life. When measuring the thermal shock resistance of the coating, the test piece is heated to the required temperature, maintained at the current temperature for a certain period of time, and then cooled to room temperature. This is a thermal shock. This is repeated until the test piece is destroyed. The number of thermal shocks experienced is the thermal shock resistance life of the coating.
It can be seen from the above table that the T7# coating is more stable than other coatings, and all performances can meet the design requirements. It is the most suitable high-temperature oxidation resistance coating for Ta10W alloy. The static oxidation resistance and thermal shock resistance of Ta10W alloy after coating are very good in the atmosphere, and the high temperature oxidation resistance is greatly improved. The gold coating is improved in the later stage. The improved coating performance is shown in Table 3.
3 Application
Tantalum alloys, such as tantalum-tungsten alloy and copper-hafnium alloy, can be used as heat-resistant and high-strength structural materials for supersonic aircraft, rockets, and missiles, as well as parts of control and regulating devices. For example, the combustion chamber of the American Agena spacecraft is made of Ta10w alloy, and the nose cone of the missile engine has also used Ta10W alloy. This alloy has a melting point of 3080℃, and has high temperature toughness and impact resistance. It can be used at 2500℃ and can be used as the combustion chamber of the spacecraft, the nose cone of the missile engine, the nozzle, the exhaust pipe and other important parts. Ta10w alloy is used in the gas generator valve assembly in the Trident boost control system, the extendable nozzle in the third stage of the MX missile, the dual propellant reaction control R-4D rocket engine, the combustion chamber wall of the "Apollo" spacecraft (working temperature 1704℃), the high-temperature materials of small liquid rocket engines, the heat-resistant skin of winged lift vehicles, and the regenerative cooling nozzle of rocket engines. In addition, tantalum alloys are also used in the engine rudders of the anti-tank missiles designed by my country and the infrared source at the tail of the missile.
The application of tantalum alloy in the aerospace industry mainly has three aspects: solid propellant rockets; re-entry vehicles; devices for containing liquid metals in the power system. Solid propellant rockets have very high flame temperatures in the combustion chamber (up to 2760℃). Since the combustion products are reducing, the use of refractory metals and their alloys with poor oxidation resistance as rocket nozzles will not damage their working performance. When the aircraft re-enters the atmosphere, due to the long duration of strong heat flow, the wing surface of the aircraft can be made of refractory metal materials. For example, Ta10W alloy is suitable for the skin of reentry vehicles because the temperature of the skin exceeds 1426℃. In aerospace nuclear power systems, it is mainly used to hold liquid metals. Liquid metals are often used as heat carriers in nuclear reactors to transfer heat from the reactor to turbines and engines. Tantalum and niobium-based alloys are ideal materials for holding liquid metals, which are resistant to high-temperature corrosion.
In 2007, China's aerospace industry successfully completed the launch of the "Long March" carrier rocket for 100 times, delivered the "Nigeria Communications Satellite No. 1" on orbit, and built a new Hainan aerospace launch terminal, information kiosk, multimedia telephone, personal computer, electronic billboard and other fields. All ten launch missions were successful. The successful implementation of the first lunar exploration project also marks that China's aerospace industry has entered a new era of deep space exploration.
As an excellent high-temperature alloy, Ta10w will be more widely used in the aerospace field, and the successful development of a matching high-temperature anti-oxidation coating will further improve the high-temperature anti-oxidation performance of the alloy, enabling it to break through its own limitations and play a greater role in the aerospace industry.
About Stardust Technology
Stardust Technology (Guangdong) Co., Ltd. is a national high-tech enterprise specializing in the research, development, production and sales of high-end spherical powder materials for 3D printing, powder metallurgy, surface engineering and other fields. The company insists on taking radio frequency plasma spheroidization powder making technology as the core, and provides internationally advanced powder products and application solutions.
The company's main products include high-end rare refractory metals such as tungsten, molybdenum, tantalum, niobium, vanadium, rhenium, chromium and their alloys, compound spherical powders. At the same time, it provides technical services such as radio frequency plasma spheroidization, plasma rotating electrode atomization, 3D printing, hot isostatic pressing, injection molding, powder metallurgy, etc.
The spherical Ta-W refractory alloy powder produced by Stardust Technology is made by radio frequency plasma spheroidization atomization method, which has the characteristics of high purity hypoxia, high sphericity, smooth surface, no satellite, uniform particle size distribution, excellent flowability, high loose density and vibration density. Tantalum tungsten alloy is a high-density material with high melting point, high tensile strength, good dynamic ductility and corrosion resistance. It is used in chemical corrosion protection, machinery, aerospace and military fields.https://www.stardustpowder.com/spherical-ta-w-alloy-powder
For more details, please contact us
Source: China Library Classification Number: TG174 Document Identification Code: A Article Number: 1671-7597 (2012) 0810082-02