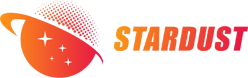
Porous tantalum is a foamy porous metallic material with a similar pore structure to human bone. Compared with other medical metal materials, porous tantalum has high volumetric porosity, low modulus of elasticity and high surface friction coefficient, which is an ideal bone replacement material [1], and its application prospect is expected to catch up with titanium alloys, which are the most widely used in clinical applications, and become a new direction in the research of orthopaedic clinical application materials [2].The porous tantalum implant prepared by gas-phase deposition technology by Zimmer [3] has already been used in clinical applications on a large scale, with 15-year follow-up results for 52 patients showing no cases of inflammation. The porous tantalum implant prepared by Zimmer [3] using the gas phase deposition technology has been applied in clinical scale, and the 15-year tracking results of 52 patients showed that none of them had problems such as inflammation, implant loosening, bone resorption, and acetabular dislocation, and none of them needed to re-implement acetabular revision, which fully proved the stability of the porous tantalum implant in the early stage of clinical application and in the long term.
With the popularity of the concept of precision medicine, the clinic has put forward personalised demand for implants, how to solve the problem of the lack of individual matching of standardised implants has become a topic of common concern and a research hotspot in the medical and engineering communities [4]. The emergence of additive manufacturing technology has made the industrial preparation of personalised implants a reality and has been successful in the fabrication of titanium implants [5]. The results of existing studies have shown that spherical powders with excellent flowability and high packing density are the preferred raw materials for additive manufacturing technology [6]. However, due to the high melting point of tantalum metal (2996°C), it is difficult to prepare spherical tantalum powder by traditional spherical powder preparation processes (e.g., aerosolisation method); on the other hand, the traditional preparation processes of tantalum powders for capacitors, such as sodium potassium fluorotantalate reduction method, hydrogenation crushing, etc., the powders obtained have too small a particle size (<10 μm), complex shapes, and are basically without liquidity, which can't meet the technological process requirements for additive manufacturing [7].
Radiofrequency plasma is an excellent method for the preparation of spherical powders with uniform components, high sphericity and good fluidity due to the advantages of high temperature (about 104°C), large plasma torch volume, high energy density, basically no pollution, and fast heat transfer and cooling [8]. Especially in the high melting point, refractory metal spherical treatment, the high temperature generated by the radio frequency plasma can provide enough energy to make the refractory metal powder in the plasma across the rapid heat absorption, melting, and condensation under the action of surface tension into a spherical shape, in a very short period of time, the sudden cold condensation to form a spherical powder, is to obtain the density of high, spherical degree of good purity of the spherical powder of an effective means of larger than the other process has a greater It has greater technical advantages than other processes. Domestic and foreign scholars have successfully prepared spherical W, Mo and other refractory metals as well as alumina ceramic powders by using RF plasma technology [8-10], while the preparation of spherical tantalum powder by using RF plasma has not been reported. In this paper, the metallurgical grade tantalum powder is used as raw material, and the spherical tantalum powder for additive manufacturing is prepared by RF plasma spheroidisation technology, and the effects of spheroidisation treatment process on the powder characteristics and the effects of charging rate on the spheroidisation rate are investigated with a view to providing a basis for the preparation and application of spherical tantalum powder.
1 Experimental materials and methods
1.1 Raw materials and spheroidisation device
The experimental raw materials were metallurgical grade tantalum powder provided by Ningxia Oriental Tantalum Industrial Co.
The raw tantalum powder was spheroidised using a TekSphero 40 RF plasma system (TeknaCo. Ltd. Canada), and the spheroidisation device is shown in Figure 1. The system mainly includes RF plasma torch, programmable logic controller (PLC), RF generator, powder supply system, vacuum system, powder collection chamber and water cooling system. The experiment uses high purity argon as the plasma gas to generate plasma under the excitation of electric field, and high purity argon is used as the sheath gas to cool the quartz tube of the plasma system. The powder raw material is fed into the plasma torch through helium (carrier gas) at a constant supply rate, during which the powder particles are rapidly melted and undergo a solid-liquid phase transition, and the liquid particles are spheroidised and solidified under the drive of surface tension, and finally collected in the powder recycling tank.The process parameters used for the experiment are shown in Table 1.
Fig.1 Structural schematic diagram of plasma spheronisation device
Table1ProcessingparametersforRFplasmaprocessingtantalum powder
1.2 Performance testing
Scanning electron microscope (JEOL, JSM-6460, scanningelectronmicroscope, SEM) was used to observe the morphological changes of tantalum powder before and after spheronisation, and at least 10 fields of view were selected for the statistics of powder sphericity at different supply rates under the same magnification. The particle size distribution of the powders was analysed using a Malvern laser diffraction analyser (MalvernMS2000, Worcestershire, UK). The phase composition of the powders was characterised by X-ray diffraction (BrukerD8AdvancePhaser, X-raydiffraction, XRD). The flowability and bulk density of tantalum powders were measured using a Hall flow meter according to ASTMB213-13 and ASTMB212-13, and at least three points were determined for each set of data and averaged. Atomic emission plasma spectroscopy was used to determine the changes of C, H and O elements of tantalum powder before and after spheronisation.
2 Results and Discussion
2.1 Influence of spheronisation process on powder spheronisation efficiency
RF plasma has been successfully used for the spheroidisation of high melting point refractory powders such as W, Nb, Al2O3, etc. The results of the study show that the powder supply rate is a key factor in determining the spheroidisation efficiency [8-11]. Therefore, this paper focuses on the effect of powder supply rate on the spheroidisation efficiency of tantalum powder, and other process parameters are referred to the suggested values provided by equipment suppliers as shown in Table 1.
The morphology of tantalum powder after spheroidisation at different supply rates is shown in Fig. 2. It can be seen that when the powder supply rate is 10g-min-1, the spheroidised tantalum powder shows good dispersion, and the spheroidisation rate is 91%. Figure 3 shows the effect of powder supply rate on the spheroidisation rate of tantalum powder, with the increase of the supply rate, the spheroidisation rate of the powder decreased from 91% to less than 20%, and only a small part of the particles were spheroidised when the supply rate was increased to more than 40g-min-1.
Fig.2SEMimagesofthespheroidizedtantalumpowdersatdifferentfeedingrates:(a)rawpowders; (b)10g-min-1; (c)20g-min-1; (d)30g-min-1; (e)50g-min-1; (f) 50g-min-1
Fig.3 Influence of powder supply rate on spheroidisation rate of tantalum powder
The energy required for complete globalisation of tantalum powder particles can be calculated according to equation(1) to calculate [12].
Where: Q is the energy required to melt all the tantalum powder, v is the powder feed rate during spheronisation, d is the diameter of the powder particles, ρ is the density, Cp is the specific heat capacity, Tm is the melting point, T0 is the ambient temperature, and Hm is the latent heat of melting of tantalum. It can be seen that an increase in the powder feed rate will result in an increase in the amount of heat required per unit time, and that coarse particles require more energy than fine particles. Therefore, under the process parameters used in this paper, the energy gained by the powder is sufficient to melt the tantalum powder being fed into the plasma region when the supply rate is 10 g-min-1, when the powder particles have the highest sphericalisation rate. As the powder supply rate increases, the amount of thermal energy available to a single powder particle under certain conditions gradually decreases, leading to a rapid decrease in the spheroidisation rate of the powder. On the other hand, too large a supply rate may also cause the trajectory of some particles to deviate from the high-temperature region of the plasma, which leads to underutilisation of energy [13] and also reduces the spheroidisation rate of tantalum powder.
It was also found in Fig. 2 that large-size particles are more likely to be spheroidised than small-size particles (<5 μm) at higher supply rates.A similar phenomenon was observed by Yu et al [14] in the spheroidisation of tungsten powders by RF plasma. This may be due to the "anti-mixing" effect that occurs during plasma spheronisation of small-sized powder particles, which escapes the small particles from the high temperature region [15], resulting in poorer spheronisation of small-sized powders.
2.2 Influence of spheroidisation parameters on the physical properties of tantalum powder
In order to ensure the stability of the process and the quality of the formed parts, the powder feedstock required for additive manufacturing technology usually has a high bulk density (more than 50% of the theoretical density) and good flowability. For commercial metallurgical grade tantalum powder, the bulk density is only 35% of the theoretical density, and the raw material powder has almost zero flowability due to the fine particle size, strong van der Waals forces between powders, serious powder agglomeration, and serious bridging between irregularly shaped powders. The effect of powder supply rate on the physical properties (flowability and bulk density) of plasma spheronised tantalum powder is given in Figure 4. As can be seen from the figure, the flowability of tantalum powder was significantly improved after plasma spheroidisation; when the powder supply rate was 10 g-min-1, the obtained loose loading density of tantalum powder reached 56% of the theoretical density, and the flowability reached 13.83 [s-(50 g)-1]. This is due to the small contact surface when spherical powder particles are stacked after spheroidisation, the gap between particles is reduced, and the bridging phenomenon is significantly reduced, so that the loose loading density and vibration density are significantly improved, and the requirements of additive manufacturing technology are met.
Fig.4Influence of powder supply rate on tantalum powder fluidity and loose loading density
2.3 Effect of spheroidisation treatment on powder particle size and particle size distribution
The test results of the particle size distribution of tantalum powder before and after spheronisation are given in Figure 5. It can be seen that the particle size distribution of the metallurgical grade tantalum powder raw material is wide, with an average particle size of 12 μm. when the powder supply rate is 10 g-min-1, the particle size distribution of the spheroidised tantalum powder changes slightly, and the average particle size increases to 15 μm. this is due to the fact that in the process of plasma spheroidisation, particles of smaller sizes will collide with each other after melting, bonding, and then grow into particles of larger sizes. In addition, there is a possibility of localised over-melting of the smaller sized particles, leading to their vaporisation and condensation on the walls of the spheronisation chamber. As a result, the amount of small-sized powder in the ultimately collected spherical powder is reduced, and the particle size distribution of the sphericalised tantalum powder is more concentrated. In addition, from the above analysis, it can be seen that the particle size of the spherical powder prepared by plasma spheroidisation and its distribution are mainly determined by the original powder particle size, so in order to obtain a spherical powder with a narrow particle size distribution, the particle size distribution of the original powder should be strictly controlled.
Fig.5 Particle size distribution of tantalum powder before and after spheronisation
2.4 The effect of spheroidisation on the composition of the powder and the composition of the physical phase.
The content (mass fraction) of impurity elements in tantalum powder before and after spheroidisation is shown in Table 2. The content of interstitial elements in tantalum powder before and after spheroidisation did not change significantly due to the atmosphere protection throughout the spheroidisation process. In addition, the X-ray diffractograms of tantalum powder before and after spheronisation in Fig. 6 show that no other phases appeared in the tantalum powder after spheronisation, which fully verified the feasibility of the RF plasma spheronisation technique for the preparation of spherical tantalum powder. Figure 7 gives the surface morphology and cross-section photos of the spherical tantalum powder after spheronisation. As shown in the figure, the surface of the spherical tantalum powder after spheroidisation is bright and clean, with good sphericity; no hollow powder defects were found in the cross-section inspection of the powder, which fully ensures the process stability during additive manufacturing and the reliable quality of the formed parts.
Table 2 Mass fraction of impurity elements of tantalum powder before and after spheroidisation
Fig.6 X-ray diffraction of tantalum powder before and after spheroidisation
3 Conclusion
(1) The preparation of spherical tantalum powder for additive manufacturing was successfully achieved by using RF plasma spheroidisation technology with irregular-shaped commercial metallurgical-grade tantalum powder as raw material.
(2) The powder supply rate is the key process parameter that determines the effect of powder spheroidisation. When the powder supply rate is 10g-min-1, the spheroidisation rate of tantalum powder can reach more than 90%, and at this time, the fluidity of tantalum powder is 13.83[s-(50g)-1], and the bulk density is 58%, which meets the requirements of additive manufacturing technology.
(3) After spheroidisation, the content of interstitial elements in the tantalum powder did not increase significantly, the surface of the powder was smooth, and no defects such as hollow powder were found inside.
Fig.7Surface (a) and cross-section (b) micro-morphology of spheroidised powder
References:
Article source:https://pmt.ustb.edu.cn/cn/article/doi/10.19591/j.cnki.cn11-1974/tf.2020.02.009
Stardust Technology (Guangdong) Co., Ltd. is a high-tech enterprise specialising in the research, development, production and sales of high-end spherical powder materials in the fields of 3D printing, powder metallurgy and surface engineering. The company adheres to RF plasma spherical metal powder technology as a guide to provide international advanced products and application solutions.
The company's main products are spherical tantalum powder and tantalum alloy powder, spherical tungsten and tungsten alloy powder, spherical molybdenum and molybdenum powder, spherical niobium and niobium alloy powder, spherical titanium and spherical titanium alloy powder, spherical refractory high entropy alloy powder, high-end rare refractory metals and composite spherical powders, and to provide radio-frequency plasma spheroidisation services, plasma rotating electrode atomisation services. 3D printing services, hot isostatic pressing, injection moulding, powder metallurgy and other technical services.
Refractory metal powder and other consulting, welcome to contact our
sales manager :Cathie Zheng + 86 13318326187.
we will be enthusiastic for you to answer.