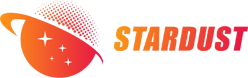
With excellent properties such as high density, high melting point, high strength, low coefficient of thermal expansion, good corrosion resistance and thermo-electronic emission capability, tungsten metal has been widely used in many industrial and defense fields such as aerospace, military industry and electronics industry [1-5]. Spherical tungsten powder has good fluidity and high bulk density, and has received more and more widespread attention in industrial production. In the field of thermal spraying, spherical tungsten powders, due to their good fluidity, prepare coatings that are more homogeneous, dense, and have good wear resistance [6,7]. In addition, porous tungsten cathode materials prepared with spherical tungsten powder have more uniform pores and will replace conventional tungsten powder for the preparation of porous tungsten parts [8]. In the field of powder metallurgy, spherical tungsten powders have high bulk density and shrink very uniformly during sintering for good dimensional control [9].
Radiofrequency plasma has the advantages of high temperature (about 104°C), large plasma torch volume, high energy density, and fast heat transfer and cooling, which is a good way to prepare spherical powders with uniform components, high sphericity, few defects, and good flowability [10-12]. Using plasma as a heat source, it has a large technical advantage in spheroidization treatment of refractory metals [13]. Radio frequency (RF) plasma in the process of spheroidizing powder, its high temperature provides enough energy to make the powder in crossing the plasma quickly absorb heat, melt, and condense into a spherical shape under the action of surface tension, and in a very short period of time sudden cold solidification, resulting in the formation of a spherical powder. The plasma melting spheronization technique is considered to be one of the most effective means to obtain dense, regular spherical powders.
In this experiment, tungsten powders with different particle sizes and irregular shapes were used as raw materials to prepare spherical tungsten powders by radio frequency plasma spheronization. The process of preparing spherical tungsten powder is mainly studied, and the influence of charging rate on the sphericalization rate of powder is analyzed.
1 Experiment
The experiment used tungsten powder with Fischer's size of 5.5, 11.5 and 26.5 μm as raw material, and the shape of the powder was irregular. The RF plasma device used for the preparation of spherical tungsten powder mainly includes a RF induction plasma generation system with a frequency of 3.5 MHz and a rated power of 100 kW; a cooling chamber, a feeding system and a product collection system, as shown in Fig. 1.
The device uses argon as the working gas to establish a stable operation plasma torch, and uses argon as the carrier gas to feed the tungsten powder into the plasma arc axially through the feeding system and the charging gun, and the position of the powder into the plasma is located in the second circle of the induction coil. In the process of plasma spheronization, the powder particles pass through the high temperature zone of plasma to absorb heat, melt and spheronize instantly, and then enter the cooling chamber to condense rapidly to form spherical tungsten powder, and the spherical powder is obtained through the collection system, and the detailed process parameters are listed in Table 1.
The phase composition was detected by D/MAXRB X-ray diffractometer from Rigaku, Japan; the morphology and microstructure of the powder were observed by LEO-1450 scanning electron microscope; the particle size and particle size distribution of the powder were tested by LMS-30 laser particle size analyzer from Fresh, Japan; and the bulk density and fluidity of the tungsten powder were determined by Hall flow meter.
2 Results and Discussion
2.1 Plasma spheroidization of irregular tungsten powder
Figure 2 shows the SEM photographs of irregularly shaped tungsten powders with particle sizes of 5.5 μm (Figs. 2a1,b1), 11.5 μm (Figs. 2a2,b2) and 26.5 μm (Figs. 2a3,b3) before and after RF plasma spheroidization treatment. As can be seen from Fig. 2, tungsten powder with smooth surface and high sphericity was obtained after plasma spheroidization treatment (shown in Fig. 2b1,b2,b3). And the powder dispersion is good, the agglomeration phenomenon disappears, and the spheroidization rate can reach 100%.
In the experiment, it was found that the powder after spheroidization treatment contained abnormally large spherical tungsten powder. Figure 3 shows the laser particle size distribution of tungsten powder before and after spheronization treatment. From the figure, it can be seen that the average particle size of raw tungsten powder is 19.36 μm, and 80% of the powder particle size distribution is between 10 and 35 μm. After plasma spheronization treatment, the average particle size is 33.59μm, and the particle size increases. Due to the agglomeration phenomenon of raw material powder, and the agglomerated powder was not sufficiently dispersed during the spheronization treatment, resulting in its overall melting and spheronization to form large particles of spherical tungsten powder. In addition, in the process of plasma spheroidization, due to the disorder of the trajectory of some powders, the molten tungsten powders collide with each other when crossing the plasma, forming large particles of tungsten powder (shown in Figure 4).
Figure 5 shows the SEM photograph of the cross section of the spherical tungsten powder (26.5 μm). As can be seen from the figure, the irregularly shaped corners of the original tungsten powder have been eliminated. The dense internal structure of the spherical tungsten powder indicates that the powder fully absorbed heat during the plasma spheronization process, and the surface or the whole was melted to realize the densification of the powder. The length-to-diameter ratio of the spherical powder is close to 1:1, and the sphericity of the powder is good and regular.
The XRD patterns of tungsten powder before and after RF plasma treatment are shown in Fig. 6. From the XRD patterns, it can be seen that the position of the diffraction peaks of the spherical tungsten powder is the same as that of the raw tungsten powder, and there is no change, and the characteristic diffraction peaks (110), (200), (211) and (220) characterize the powder as a body-centered cubic (bcc) structure. A single W phase was present before and after spheronization, and no diffraction peaks characteristic of other impurity phases appeared. Single-phase tungsten powder can be prepared after RF plasma spheronization using argon as the plasma working gas.
2.2 Influence of charging rate and powder size on powder spheroidization rate
In the RF plasma spheroidization process, the process parameters, especially the charging rate, have an important effect on the spheroidization of tungsten powder. Under the same process parameters, different charging rate, the spheroidization effect of powder is different. Figure 7 shows the effect of charging rate on the spheroidization rate of powder. As can be seen from Figure 7, the spheroidization rate of powder decreases with the increase of charging rate for tungsten powders of different particle sizes. When the charging rate is greater than 25g/min, the spheroidization rate of the powder decreases significantly. Due to the increase in charging rate, more powder passes through the plasma per unit time, and the heat required for powder spheronization increases. However, the heat provided by the system under fixed process conditions is a fixed value, which cannot meet the needs of heat absorption, melting and spheroidization of excess tungsten powder, resulting in a decrease in the spheroidization rate of the powder. In addition, the increase in charging rate causes the running trajectory of part of the powder in the plasma to deviate from the high-temperature zone of the plasma, and the heat absorption of the powder is not sufficient, which ultimately leads to the decrease in the spheroidization rate of the powder. Under certain process conditions of the system, a reasonable charging rate is an important factor to ensure the powder spheroidization rate.
From Figure 7, it can also be seen that when the charging rate is certain, the spheroidization rate decreases with the increase in the particle size of the powder. The powder with smaller particle size has a larger specific surface area and absorbs heat more fully when crossing the plasma, which is conducive to the spheroidization of the powder. Generally speaking, as the particle size of the powder decreases, its melting point also decreases, and it is easier to absorb the same energy for spheronization. Therefore, under the same process parameters, the spheroidization rate of smaller powder size is higher.
SEM photographs of spheroidized powder prepared from 26.5 μm tungsten powder with different charging rates are given in Figure 8. As can be seen from the figure, the spheroidization rate of tungsten powder reaches more than 95% when the charging rate is 5g/min (Fig. 8a) and 10g/min (Fig. 8b). When the charging rate was increased to 15g/min (Fig. 8c) and 20g/min (Fig. 8d), the spheroidization rate of tungsten powder could still be maintained above 80%, with the spheroidization rate of 15g/min being 90%. When the charging rate was increased to 25g/min (Fig. 8e) and 30g/min (Fig. 8f), the spheroidization rate of tungsten powder was 70% and 50%, respectively.
2.3 Loose loading density and flowability of tungsten powder before and after spheronization
Figure 9 shows the effect of spheroidization rate of 26.5μm tungsten powder on the bulk density and flowability of the powder. As can be seen from the figure, with the increase of tungsten powder spheroidization rate, the bulk density is also gradually improved, and the powder flowability is greatly improved. When the spheroidization rate of tungsten powder is increased from 0 to 100%, the bulk density of the powder is increased from 6.80g/cm3 to 11.5g/cm3, and the powder flowability is improved from 14.12s/50g to 6.95s/50g.
The main factor affecting the powder bulk density is the morphology of the particles. Spherical particles are stacked with small contact surfaces, reduced bridging phenomenon, and fewer inter-particle voids, which is conducive to the improvement of stacking density. The higher the degree of powder sphericity, the greater the bulk density. Therefore, spherical tungsten powder has a high bulk density. The fluidity of the powder is directly related to the morphology and particle size. The more regular and smooth the morphology of the powder, the smaller the contact area of the powder, the lower the friction, the higher the fluidity of the powder. After spheronization, the shape of tungsten powder becomes regular spherical, which is conducive to the improvement of powder bulk density and fluidity.
3 Conclusion
1) Single-phase spherical tungsten powder can be obtained by RF plasma treatment. The surface of spherical tungsten powder is smooth, the sphericity is good, and the sphericalization rate can reach 100%. The particle size of tungsten powder increased slightly after spheronization treatment.
2) The charging rate is an important factor affecting the spheroidization rate of the powder. Under the same process parameters, with the increase of charging rate, the spheroidization rate of tungsten powder decreases. The spheroidization rate of tungsten powder with smaller particle size is higher.
3) With the increase of spheroidization rate of tungsten powder, the bulk density and flowability of the powder were improved. The bulk density of tungsten powder was increased from 6.80 g/cm3 to 11.5 g/cm3, and the powder flowability was improved from 14.12 s/50g to 6.95 s/50g.
reference:Rare metal materials and engineering, vol. 40, no. 11.Preparation of spherical tungsten powders by radiofrequency plasma
Spherical tungsten powder prepared by Stardust Technology using RF plasma spheronization technology has high purity, low oxygen, high sphericity, smooth surface, no satellite balls, very few hollow particles, uniform particle size distribution, excellent flowability properties as well as high bulk density and vibration density. Tungsten has excellent high temperature resistance and ray shielding properties, and is also widely used in the defense industry, medical equipment and other fields. Spherical tungsten powder is suitable for laser/electron beam additive manufacturing, laser direct deposition, hot isostatic pressing, injection molding, laser cladding and other processes.
For more details, please contact our professional Manager Cathie Zheng +86 13318326187