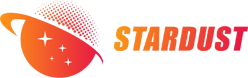
0 Introduction
Molybdenum belongs to the VIB group of elements, atomic number 42, relative atomic mass 95.95, extra-nuclear electron arrangement [Kr] 4d5 5s1, ionisation energy 7.5 eV, relative density 10.2 g/cm3 , melting point 2622, specific heat 0.28 J/(g -K), thermal conductivity 142.1W/(m -K), coefficient of thermal expansion 5.3×10-6/K, molybdenum has a body-centred cubic Molybdenum has a body-centred cubic structure, with a more obvious plastic - brittle temperature. With the continuous development of optoelectronics and thin film technology, high purity molybdenum due to its high melting point (2625 ℃), high thermal conductivity, good corrosion resistance, low specific impedance, good resistance to thermal shock and thermal fatigue properties, good toughness and ductility, medium hardness and other characteristics of molybdenum as a molybdenum target through sputtering deposition of various types of substrate surface to form a sputtering film, widely used in a variety of electronic products. Such as high-voltage high-current semiconductor devices, molybdenum leads, audio-visual equipment, camera parts, high-density integrated circuits in the gate electrode, high-precision electronics industry, thin-film transistor liquid crystal display (TFT-LCD) and new thin-film solar cells, and so on. In addition, high-purity molybdenum can also be used for rocket nozzles, catalysts, chemical reagents and so on.
The electronic properties of molybdenum depend largely on its purity, which directly affects the application. For example: the field of flat panel display and solar cell field of raw material molybdenum powder purity requirements of the quality fraction of 99.99% (4N) or more, the integrated circuit field with high purity molybdenum powder purity requirements of 99.999% (5N) or more. In the electronics industry, alkaline metal elements such as Na and K ions are prone to drift in the insulating layer, affecting its electrical conductivity; radioactive elements such as uranium (U) and thorium (Th) and other elements will release natural α-rays caused by soft breakdown of the device; Fe, Ni and other elements to affect the film shaping, thereby generating interfacial leakage; gaseous elements, such as the O element to affect the film's electrical resistivity [1-2], the non-metallic elements S, C etc., are easy to form MoC with molybdenum in high temperature environments, leading to wear cracking of high-purity molybdenum. Therefore, these harmful impurity elements must be strictly removed to improve the purity of molybdenum metal as raw material, so as to ensure the high precision and large uniformity required by the electronics industry.
At present, industrial mass production of molybdenum powder purity of 99.95%, far less than the requirements of the microelectronics industry, before the report on high-purity molybdenum powder is mainly focused on the Japanese Tokyo Tungsten, Toshiba, Hitachi, Germany's Stantec and Austria's Plansee, etc., the Japanese Toshiba company φ100μm ammonium dimolybdate as raw material, through the hydrogen reduction to get the ordinary molybdenum powder, through the hydrogen peroxide to oxidise the molybdenum powder. Hydrogen peroxide oxidises and dissolves molybdenum powder into molybdic acid solution, which is then purified by cation exchange resin and dried to obtain high-purity molybdenum trioxide, crushed to 5-20μm, and ultimately hydrogen-reduced by special molybdenum layer-lined reduction equipment to obtain high-purity molybdenum powder with 5N~5N5[3], and the flowchart is shown in Fig. 1.
Germany H.C. Starck company used moving bed with ammonium dimolybdate as precursor system to produce molybdenum powder with a particle size of 2.3μm[4], and then processed to obtain high purity molybdenum powder with a purity of 5N by pressing and sintering. Berlin, Germany Hermann Stark company used special equipment in the 10 absolute clean room to successfully increase the purity of molybdenum powder to more than 6N, the current annual production capacity of the production line for 2.5t. Austria Plansee production of molybdenum powder purity of 99.97% (counting tungsten), and its production of molybdenum sputtering target purity can reach 4N. China as the most important molybdenum reserves and producers, although molybdenum resources, but mainly produces molybdenum in the production of molybdenum, molybdenum and molybdenum powder. China, as the most important molybdenum reserves and producer, although rich in molybdenum resources, but mainly produces primary molybdenum products, high value-added products, accounting for a low share of global molybdenum industry profits. At present, there are a large number of domestic researchers working on high purity molybdenum. Academician Zhao Zhongwei's team at Central South University has developed a high purity molybdenum powder with a purity of 99.995% (4N5) (counting tungsten content), which can be kilogram produced in the laboratory, and is currently undergoing industrialisation tests. Jinduicheng Molybdenum Industry Co., Ltd Metal Branch has achieved an annual production capacity of 1000t of 4N molybdenum powder in 2023.In recent years, China's preparation of high purity molybdenum has made great progress, but still lack of systematic research.
This paper introduces the existing preparation technology of high purity molybdenum powder, points out some problems in the current research, and analyses its application prospects.
1 high purity molybdenum powder preparation technology
At present, the main methods for the production of high purity molybdenum metal [5] are: (1) improve the purity of raw materials for the preparation of molybdenum metal - molybdenum compounds. For example: high purity ammonium molybdate or high purity MoO3 through high purity hydrogen reduction or carbon reduction to obtain high purity molybdenum powder; high purity MoCl5 through hydrogen plasma flame reduction or hydrolysis, drying to obtain MoO3 and then reduce to obtain high purity molybdenum powder; high purity Mo(CO)6 steam thermal decomposition to obtain high purity molybdenum and so on. (2) Ordinary molybdenum powder is processed and purified to prepare high-purity molybdenum. The main methods include: electron beam melting, plasma spheroidisation and so on.
1.1 Improve the purity of raw materials for the preparation of molybdenum metal - molybdenum compounds
1.1.1 High-purity MoO3 reduction method
Preparation of high-purity molybdenum raw materials are generally ammonium dimolybdate (ADM) or tetramolybdate (AQM), molecular formula (NH4)2Mo2O7, (NH4)2Mo4O13. first, ammonium molybdate heating and roasting to lose water of crystallization, ammonia volatilization, to get the MoO3, and then the reduction of hydrogen or carbon reduction of MoO3, water vapour or CO2 volatilization to get the molybdenum metal powder. Figure 2 for ammonium dimolybdate, molybdenum trioxide and molybdenum powder morphology. The preparation of chemical equations as shown in the formula (1)~(4).
Therefore, the first condition for the preparation of high-purity molybdenum is to purify high-purity ammonium molybdate or high-purity MoO3, and the methods of purifying ammonium molybdate or MoO3 include sublimation, precipitation, solvent extraction, ion exchange, crystallisation, etc. Sublimation: using the characteristics of MoO3 sublimation above 600℃ to produce pure MoO3, the purity of MoO3 can reach more than 3N5.
Sublimation method: Using the characteristics of MoO3 sublimation above 600 ℃ to produce pure MoO3. sublimation temperature of 600-1000 ℃, MoO3 purity can reach more than 3N5. If the temperature is too high, the impurities in the raw material will also be sublimated and evaporated into the MoO3 [6]. Climax company in the United States was the first to use sublimation method to produce pure molybdenum trioxide, the company Moiseev et al [7] developed a new type of sublimation furnace, first of all, molybdenum oxide into the sublimation furnace, in a certain degree of vacuum, 550-580 ℃ conditions, sublimation of molybdenum oxide powder in the volatile compounds such as selenium oxide, antimony oxide, sulphur dioxide and MoO3 particles on the adsorbed water and chemical crystalline water; and then in the 690-780 ° C, a certain degree of vacuum sublimation MoO3, sublimation of MoO3 cooling to 500-550 ° C, collected made of pure MoO3, light green needle-like crystals, purity can be up to 4N5. sublimation method is the simplest process, the twentieth century in Europe and the United States in the 1950s and 1960s is widely used, but because of the method of molybdenum oxide produced by the purity of the fluctuation is large, can not be standardised, and the physical properties of the more However, due to the fluctuation of the purity of molybdenum oxide produced by this method, it is impossible to standardise the production, and there are more defects in the physical properties.
Precipitation method: according to the molybdenum and impurities of different properties, adding different precipitants, so that molybdenum and impurity ions separation method. For example, sulfide precipitation method in addition to copper, iron, lead, etc.; magnesium salt precipitation method in addition to phosphorus, arsenic, silicon, etc. [8-9]; iron salt precipitation method in addition to tungsten, etc.. Yang Liang et al. used ammonium magnesium salt precipitation method to make the arsenic in ammonium molybdate solution to form ammonium magnesium arsenate precipitation and remove. In the magnesium chloride dosage for the theoretical amount of 1.2 times, room temperature, reaction time 30min conditions, ammonium molybdate solution of arsenic mass concentration decreased to 1/170, excess Mg2+ with 724 weak acidic cation resin adsorption to remove, arsenic removal reaction as shown in the formula (5)~(6).
Tungsten and molybdenum belong to group VIB elements, due to the influence of lanthanide contraction, tungsten and molybdenum ionic radius is very close to the atomic structure and chemical properties are similar, tungsten and molybdenum depth separation is currently one of the powder metallurgy difficulties. Leng Mingfeng et al [10] used the adsorption co-precipitation method, which can be used for the ammonium molybdate solution produced by ammonia leaching method in addition to a small amount of tungsten, the specific scheme is to add Fe(NO)3-9H2O to the solution, and the tungsten is co-precipitated by the new ecological Fe(OH)3 as a carrier, and the adsorption and separation of W is best in pH=7.5~8.5, the ratio of Fe3+/W mass concentration of 6, and the aging time of 24 h. The adsorption and separation of tungsten and molybdenum is also very difficult in powder metallurgy. Compared with the extraction method and ion exchange method, the precipitation method is simple, short process flow, low production cost, but the depth of the decontamination effect is not obvious, industrially applicable to the initial purification of the original material.
Solvent extraction method: the use of compounds in two immiscible solvents in the distribution coefficient of the different compounds from one solvent to another solvent. Solvent extraction method in the preparation of high purity ammonium molybdate process, the main use of amine extractant, Figure 3 for the extraction method of purification of ammonium molybdate production of high purity molybdenum powder flow chart.Viktor et al [11] used the extraction method to purify and purify the preparation of heptamolybdenum acid ammonium molybdate, industrial molybdenum trioxide alkali leaching of the crude sodium molybdate solution obtained by adjusting the pH to 2.5, with the use of bis-tridecanamide-containing organic phase extracted molybdenum, molybdenum loading the organic phase introduced into the stirrer. The molybdenum-loaded organic phase was introduced into a stirrer, ammonia and the mother liquor of the last batch of cooled crystals were added, and the ratio of ammonia to molybdenum was adjusted to 1.2∶1, and the back-extracted solution containing 19.24% molybdenum was obtained, and then ammonium heptamolybdate was obtained by cooled crystals at 15~20℃. Yu Kening et al [12] added sulfuric acid to control the equilibrium aqueous phase pH=78 in a high molybdenum and low tungsten weakly alkaline solution, at this time, tungsten exists in the form of monomer WO- in the solution, the use of primary amine 1%~2% N1923 as an extractant, paraffin as a diluent, primary amine through the formation of molecular bonding molecular aggregates of the solvent extraction mechanism to preferentially extract tungsten, the generation of RNH2-H2WO4, to achieve the removal of trace amounts of tungsten from the molybdate solution. The removal of tungsten from molybdate solution was achieved by RNH2-H2WO4. Ning Pengge et al [13] carried out additional research for Yu Kening's test, and found that primary amine has little effect on the treatment of high tungsten and low molybdenum solution, but favours the treatment of high molybdenum and low tungsten and tungsten and molybdenum solution with comparable concentration, and the smaller the W/Mo in the solution the more favourable for the separation of tungsten and molybdenum, but absolute excess of molybdenum also inhibits tungsten extraction, when the 50g/L molybdenum and 1.0g/L tungsten mixture, the extraction agent is a composite amine (v/v), and the tungsten extraction mechanism is the same. 1.5% primary amine N1923,0.5% secondary amine 7207) + hydroxamic acid (1% hydroxamic acid BK992 or Lix984) + diluent (paraffin), the pH of the extraction solution was controlled to be 7.09, two-stage extraction, and then back-extracted with 10% sodium hydroxide solution, the tungsten and molybdenum separation coefficient reached 105.Zhang Guiqing et al [14] used 10% quaternary ammonium salt N263 as the extractant and 20% sec-octanol as the polarity improver. Zhang Guiqing et al [14] used 10% quaternary ammonium salt N263 as the extractant, 20% sec-octanol as the polarity improver, 70% sulphonated kerosene as the diluent, and mixed the three as the organic phase, and alkaline crude sodium molybdate solution according to a certain ratio of multi-stage countercurrent extraction, molybdenum extracted into the organic phase, and the impurities of phosphorus, arsenic and silicon were discharged with the residual extract. The loaded organic phase is washed with deionised water and then counter-currently re-extracted with ammonium carbonate solution to obtain ammonium molybdate solution with higher purity. Extraction method has been commonly used in the rare metal industry because of its fast equilibrium speed, good separation effect, large processing capacity, easy to operate continuous automation, safety and convenience. However, the extractant is an organic solvent, which has certain toxicity, environmental protection pressure, and processing difficulties.
Ion exchange method: under a certain pH value, the use of molybdate ions and impurity ions in the ion exchange resin on the adsorption capacity of different methods to separate the two. According to the exchangeable ions on the ion exchange resin, it is divided into cation exchange resin, anion exchange resin and redox resin. The functional group of the cation exchange resin is various organic acids, and according to the acidity of the organic acids, it can be divided into strong acid-type and weak acid-type cation exchange resins, and the acid carries out the exchange reaction with other cations by H+. The functional groups of anion exchange resins are various amines, of which the functional group of strong alkaline resins is quaternary amine salts, and the functional group of weak alkaline resins is primary amines, secondary amines, and tertiary amines. The anion exchange resins themselves are all strongly basic and easily add and H+ and become positively charged so that they can bind an anion (OH-type or Cl-type), and the bound anion undergoes an exchange reaction with an anion such as molybdate. Redox resins are ions in solution that undergo a redox reaction with a functional group on the resin, thus separating them from other substances. Figure 4 shows the flow chart for the purification of ammonium molybdate by ion exchange to produce high purity molybdenum powder. Toshiba, Japan, improved the previous method by placing ordinary molybdenum powder in a polytetrafluoroethylene container with water and stirring[3],then adding 30% hydrogen peroxide to oxidise, obtaining molybdic acid solution, removing impurities by H-type cation exchange resins, evaporating and concentrating the crystals, and drying to obtain high-purity MoO3.In 2016, Song Aimou et al[15] used ammonium secammonium molybdate as the raw material, added ferric nitrate to adsorb and age, filtered out the insoluble impurities In 2016, Song Aimou et al[15] used ammonium sec-molybdate as raw material, added ferric nitrate adsorption, aging, filtered out insoluble impurities, and then passed through a D380 ion exchange column to further remove impurities, then added nitric acid, acid precipitation to obtain ammonium polymolybdate precipitation, calcined to obtain high-purity MoO3, and then obtained molybdenum powder with a particle size of 0.5-10 μm through hydrogen reduction. 2018, Gao Guanjin et al[16] used a continuous-cycle ion-exchange method to purify the process and high-purity hydrogen reduction to remove potassium, 99.95% of ammonium sec-molybdate as the raw material, and ion-exchange to remove potassium and high-purity hydrogen gas to remove potassium and potassium. In 2020, Zaoqi et al [17] purified ammonium molybdate by ion exchange and then adjusted the pH=1, then adjusted the pH=2, then adjusted the pH=2, then adjusted the pH=2, then adjusted the pH=2, then adjusted the pH=2, then adjusted the pH=2, then adjusted the pH=2, then adjusted the pH=2, then adjusted the pH=1, then adjusted the pH=1, then adjusted the pH=1, then adjusted the pH=1, then adjusted the pH=3, and then adjusted the pH=1, then adjusted the pH=1, then adjusted the pH=1, and then adjusted the pH=1. In the process of purifying ammonium molybdate to prepare high purity molybdenum by ion exchange, although the water consumption is larger and the adsorption and exchange capacity of some resins is low, it has better purification effect than the general separation methods such as precipitation and crystallisation, and the purity of the product is high, and there are many types of resins to choose from. Resin variety, can choose a wide range, its separation selectivity is good, high enrichment ratio, high degree of automation, stable product properties, resin regeneration can be reused, the process is safe and environmentally friendly, is the future industrial production of high-purity molybdenum powder raw materials of the inevitable choice.
Crystallisation: A method by which the target substance is precipitated from solution. Crystallisation of ammonium molybdate includes evaporation crystallisation where the solvent is heated to evaporate, cooling crystallisation where the temperature of the saturated solution is lowered, and acid precipitation crystallisation where acid is added to precipitate. Crystallisation results in purification of the target substance, but several recrystallisations are often required to obtain a better purification. During the crystallisation process, most of the cationic impurities in the ammonium molybdate solution, including Fe2+, Cu2+, Mg2+, Ca2+, K+, Na+, as well as the anionic impurities Cl-, SO-, and NO3-, remain in the solution and the ammonium molybdate is purified. Generally, ammonium molybdate can be recrystallised several times, purified and roasted to obtain high-purity MoO3.2022 Guo Wei et al[1] used 99.95% ammonium molybdate as raw material, roasted to obtain MoO3, ammonia leaching to obtain ammonium molybdate solution, two-stage filtration, evaporation and crystallization, and then repeated the above steps for the ammonium molybdate obtained. After two purification, roasted ultra-high purity MoO3, 5N hydrogen reduction to produce large-scale integrated circuits with 5N ultra-high purity molybdenum powder. Guo Chao et al [18] use tungsten and molybdenum with polyacid and its heteropolyacid nature of the differences in different process conditions on the ammonium molybdate acid precipitation crystallisation separation of tungsten and molybdenum, control of acid precipitation endpoint pH value of 2.5, acid precipitation before the addition of ammonium phosphate can be made to make the tungsten and molybdenum crystallisation rate of the greater difference, especially when the tungsten and molybdenum is relatively large, the separation effect is good. Because of the high content of potassium in the original ore, gold molybdenum shares in production practice, the use of many times nitric acid acid precipitation crystallisation, will effectively reduce the potassium content to ≤ 8 × 10-6, the resulting low potassium ammonium molybdate for the preparation of high purity ammonium molybdate laid a good foundation [19]. The acid precipitation crystallisation method consumes a large amount of inorganic acid, the secondary input cost is large, and it is easy to cause environmental pollution, but the effect of potassium reduction is better, and it can be used as a priority before there is no better potassium reduction process at present.
High-purity MoO3 reduction is currently the most widely used method for the preparation of high-purity molybdenum powder, and the environmental purity must be strictly ensured during the preparation of high-purity molybdenum powder by hydrogen reduction or carbon reduction of high-purity MoO3.In 2007, Wang Tao et al [20] reduced high-purity molybdate or molybdenum oxides with high-purity hydrogen using a pure molybdenum boat dish with purity ≥ 98%, and produced a high-purity electronic-grade molybdenum powder with 4N and an oxygen content below 0.1 × 10-6. 2022, Tang Xinxin et al [21] used 99.95% MoO3 as raw material, using 4N hydrogen reduction, passing 0.18 mm sieve to obtain MoO2, spraying deionised water, drying, and then secondary reduction, passing 0.075 mm sieve, to obtain the furnace molybdenum powder. Then the fluidised bed air flow classifier was used for grading, the middle second stage was taken according to the particle size to get the molybdenum powder with a particle size of 3-5 μm and a purity of 3N8. The reduction process was carried out by using a pure molybdenum or a high temperature resistant boat with a molybdenum coating sprayed on the surface.In 2023, Ren Baojiang et al[22] obtained MoO2 from a one-stage reduction of low-potassium MoO3 in muffle furnaces, and used molybdenum lanthanum in an eighteen-tube furnace for the purpose of decreasing the introduction of Fe and Ni. In order to reduce the introduction of Fe and Ni, two-stage reduction is carried out in the eighteen-tube furnace using molybdenum-lanthanum alloy boat to control the reduction temperature and hydrogen flow rate, and then cleaned and sieved, mixed and packed to obtain 4N molybdenum powder, in which the eighteen-tube furnace can effectively remove potassium, and the molybdenum-lanthanum alloy boat can further reduce the impurities of Fe, Ni, Cr, etc., and the products have a K content of ≤20 × 10-6, Fe + Ni content of ≤10 × 10-6, and a W content of ≤50 × 10-6, and the process can be used for industrialisation and batch production. In 2020, Zhang et al [23] mixed ammonium molybdate or high-purity MoO3 with carbon black in the ratio of 1:0.5-1:2, and roasted it at 400-750°C in an inert atmosphere to obtain ultrafine MoO2 containing a certain amount of carbon black, and then roasted it again at 800-1150°C to obtain MoO2 containing a certain amount of molybdenum nanocore, and then finally carried out ultrapure hydrogen Finally, ultrapure hydrogen reduction was carried out at 600-1100°C to obtain high-purity molybdenum nanopowder with an average particle size of 40-200 nm and C content of ≤0.01%. This method is low cost, simple, efficient and a good way for large-scale industrial production of molybdenum nanopowder, but the specific purity index has not been published.
1.1.2 Chloride MoCl5 decomposition method
Obtain high-purity halide process principle is: industrial molybdenum trioxide halogenation to get halide (generally MoCl5), and then at 550 ℃ fractional distillation process, so that the impurities inside the volatilisation of molybdenum 5N halide, and finally through the hydrogen plasma flame reduction or hydrolysis, to produce high-purity molybdenum powder. Wu Qiusheng et al[24] mixed molybdenum powder through argon to remove oxygen, then through Cl2 and control the flow rate, heating to 600-700 ℃ reaction, followed by cooling to get MoCl5 powder, after purification to get high-purity MoCl5. Toshiba Co., Ltd. in Japan will MoO2 and halogen reaction to generate metal halide, and then the halide produced by adding water decomposition to get MoO3, MoO3 reduction to get 4N molybdenum In 2012, Tan Xinglong et al [25] improved the above method by reacting MoO2 powder with Cl2 at 220-500°C for 50-240 min, and cooling to obtain MoO2Cl2 solid, which is a selective reaction, and other elements hardly participate in the reaction. Then ammonia leaching, roasting, to obtain high-purity MoO3, and then high-purity hydrogen reduction to obtain high-purity molybdenum powder, the purity of which can reach 5N, or even 5N5 or more. Chemical reaction formula as shown in equation (7)-(9).MoCl5, MoO2Cl2 and wet air contact will decompose to produce HCl gas, corrosive and toxic, irreversible corrosion of equipment, while affecting the quality of the product.Cl2 has a strong toxicity, in the production process is not good to control, so the metal chloride decomposition method of preparation of high purity molybdenum powder failed to get industrial application.
MoCl5 can also be prepared from molybdenum metal by chloride molten salt electrolysis [6]. Molten salt electrolysis is a method of applying electrochemical principles to produce high purity metals by using electrical energy to melt certain metal salts and use them as electrolytes for electrolysis, and it has now become an important method of industrial production of alkali metals, rare-earth metals, rare-earth alloys and other metals. With graphite as the anode and metal molybdenum as the cathode, the chloride molybdenum molten salt electrolysis method is adopted, in which molybdenum chloride is loaded into the electrolysis furnace as raw material, and due to the difference in ionic electrode potentials, the molybdenum cation obtains electrons at the cathode of the electrolysis tank to be reduced into metal molybdenum, which can remove metallic impurities and most non-metallic impurities, and the product is dendritic molybdenum powder with a purity of 99.95%. The method has the advantages of simple equipment, easy to operate, easy to achieve continuous production, but the purity of the molybdenum powder produced does not meet the needs of the electronics industry nowadays, and it needs to be improved continuously.
1.1.3 Carbonyl molybdenum Mo(CO)6 thermal decomposition method
Carbonyl molybdenum thermal decomposition method [26] is to use carbonyl molybdenum as raw material, under atmospheric pressure, 350-1000 ℃, N2 atmosphere, steam thermal decomposition treatment. It takes advantage of the decomposition of carbonyl compounds, nucleation, crystallisation and nucleus growth in the gas-phase state, and the prepared molybdenum powder has an average particle size of 24 μm,which decreases with the increase of pyrolysis temperature. In order to better reduce the carbon content, the carbonyl molybdenum was oxidised by passing air through the quartz tube furnace at 400-500°C, and then reduced under pure hydrogen at 700-800°C to obtain molybdenum metal powder. The chemical reaction formula is shown in equation (10), the molybdenum powder obtained by this method has high chemical purity and good sinterability, and this method can be used for industrialisation, but the raw materials are not easy to obtain.
1.1. 4 Other
In 2023, Gao et al [27] used 4N5 of MoS3 to produce 4N molybdenum powder by reducing it in a rotary furnace by passing 4N of H2 and N2, and the exhaust gas was pumped away from the feed end under negative pressure. The chemical reaction formula is shown in Eqs. (11) and (12).This method requires high purity of raw materials and is not suitable for large-scale production.
1.2 Preparation of high-purity molybdenum powder by treatment and purification of ordinary molybdenum powder 1.2.1 Electron beam melting method
Electron beam melting [6] is the use of high-speed movement of the electron stream bombardment of molybdenum metal, all the kinetic energy of the electron beam into thermal energy, so that the melting pool temperature up to 3000 ~ 3200 ℃, molybdenum metal melting, low melting point, high saturated vapour pressure impurities in the melting process by the vacuum pumped away, melting pool can be a longer period of time in a high vacuum, molybdenum metal can be obtained best purification effect. The impurities can be reduced by at least 80% in a single electron beam melting, and multiple melting can be used to meet the demand for high purity molybdenum. The process of electron beam melting is illustrated in Figure 5. This method has been applied to purify a variety of materials such as tungsten, tantalum, titanium, nickel and iridium. A high-purity molybdenum material with a purity of up to 6N was made by a Japanese metal company using the electron beam refining method [28]. The low number of metallic and gaseous impurities and the advantages of easy forging, rolling and welding make it more important and widely used than molybdenum produced by powder metallurgy methods.
1.2.2 Plasma spheronisation [6,29]
Induction plasma spheroidisation method is the ordinary molybdenum powder particles carried by the powder gas hydrogen into the plasma torch (plasma centre temperature up to 10,000 ℃ or more), so that it quickly melt gasification, cracking, molten particles in the role of surface tension to form a high degree of spherical droplets, and in a very short period of time to condense, so as to produce high-purity dense spherical molybdenum powder. This method is characterised by good product dispersion, high sphericity and controllable reaction atmosphere, and the whole preparation process is fast and can achieve continuous production. Figure 6 shows the schematic diagram of the induction plasma experimental device, the method is very demanding on the equipment, and the investment in industrial production is relatively high.In 2017, Liu Jintao et al [30] added binder and deionized water into 99.9% molybdenum powder to make a slurry, spray granulation, and drying to obtain molybdenum powder agglomerates, and then debinding, deblinding, sintering in H2 atmosphere to obtain granulated molybdenum powder, sieving under argon gas protection, and then plasma The molten molybdenum powder is obtained by plasma spheroidisation, and then cured by cooling at less than 30°C to obtain high-purity dense spherical molybdenum powder with purity of 4N, particle size of 30~40μm and bulk density of 6.0g/cm3. Fig. 7 shows the morphology of plasma spheroidised molybdenum powder.
The most common method of preparing high purity molybdenum powder is still the purification of molybdenum compounds at the production front end. High purity molybdenum powders are obtained by clean roasting and reduction of high purity ammonium molybdate or high purity MoO3. During the preparation process, environmental purity needs to be ensured. For example, this is done in an ultra-clean room, using one-piece moulded charging drums, using pure molybdenum or molybdenum-coated vessels, and using high-purity gases in the process. The method is relatively low-cost and easy to operate, making it easy to produce on an industrial scale. E-beam refining method can prepare molybdenum powder with very high purity through multiple refining, but E-beam refining and plasma spheronisation are more costly and require higher purity of the raw material molybdenum powder. In the production process, it is often necessary to use a variety of purification methods to achieve a better purification effect, to achieve the preparation of high-purity molybdenum powder.
2 high purity molybdenum powder application prospects
In the field of national defence, metal molybdenum and its alloys due to the high melting point and can resist high-temperature hot particle flow scouring of the best choice of materials for solid fuel rocket engines, mainly used for gas rudder piece, heat insulation screen, power nozzle and a variety of fasteners and other high-temperature components. The first wall of the nuclear fusion reactor materials need to work under the conditions of ultra-high temperature and strong thermal load, and molybdenum metal has good thermal stability, good thermal shock resistance, and can work in a high thermal load environment, while its hydrogen isotope retention is low, the erosion rate is slow, so it has become a substitute for C-C composites, such as low Z materials, new fusion experimental reactors, plasma surfaces and structural materials, molybdenum metal overcomes the low Z materials, more than the tritium retention and neutron irradiation to make its thermal conductivity. Molybdenum metal overcomes the shortcomings of low-Z materials such as high tritium retention and bad thermal conductivity due to neutron irradiation. In the field of metallurgy and machinery industry, molybdenum element as an alloy steel additive can effectively improve the hardenability and tempering stability of steel, while refining the grain, improve the distribution uniformity of carbides, and further improve the strength and toughness of steel. Molybdenum head due to its high temperature strength, can withstand stainless steel deformation of the stress generated, and does not require cooling water to reduce the temperature of the head, the wall inside and outside the temperature gradient is small. At the same time, 1 molybdenum head can wear more than 300 billets, far more than the water-cooled head (1 can only wear 1 stainless steel billet), the best economic efficiency. Molybdenum metal because it is easier than tungsten processing and manufacturing, commonly used as 1350 ℃ above the use of vacuum or inert gas protection of high temperature, furnace heaters. In the glass melting furnace, molybdenum high temperature resistance to molten glass corrosion, even if trace corrosion, its oxidation corrosion products MoO3 volatile, will not contaminate the glass, and therefore commonly used as a power supply electrode for glass melting kiln. Molybdenum can be used as a rotating anode target for X-ray tubes because of its resistance to high temperatures and its ability to produce X-rays in situ when bombarded by an electron beam to test the internal structure of materials and foci of the human body. Molybdenum is also used as a sputtering target, whereby a thin layer of molybdenum is applied to the surface of a component by various sputtering techniques, chemical vapour deposition, physical vapour deposition, etc. in order to improve the surface properties of the component.
In recent years, the refined development of the electronics industry has placed higher demands on molybdenum metal, while the discovery of new properties of molybdenum metal has promoted the development of the electronics industry, and the two have achieved mutual success. To study the intrinsic properties of molybdenum metal, it is necessary to carry out in-depth purification to remove the influence of trace or even trace impurities, so as to discover its new functions and open up new applications. High-purity molybdenum powder is mainly used in the electronics industry and high-precision industries, with very high added value in flat panel displays, solar cells and integrated circuits. With the large-scale and high-precision of flat panel displays, high-purity molybdenum (4N) has gradually become the preferred wiring material in the field of flat panel displays instead of Cr due to its lower specific impedance (1/2 of Cr). In LCD, the use of high purity molybdenum can also greatly improve the brightness, contrast, colour and life of liquid crystal displays. In the new energy industry, high-purity molybdenum (4N) is deposited by sputtering on the bottom of CIGS thin-film solar cells to form the back contact of the cell, which has a great effect on the formation, growth and morphology of CIGS thin-film crystals. In the field of large-scale integrated circuits, the use of ultra-high purity molybdenum (5N) as a wiring material has become a new trend due to the low stress, high-temperature stability, and good electrical conductivity of the film formed by molybdenum. Domestic high-purity molybdenum powder is in the research and development stage, the development of 5N, 6N level or even higher purity molybdenum powder will make up the chain of molybdenum powder products, can break the head of foreign molybdenum enterprise's technological monopoly, to fill the domestic internal control, to achieve the basic raw materials in the field of electronic information of the independent guarantee supply, social benefits are significant.
3 Prospect
High-purity molybdenum has a very broad application prospect in the future development of science and technology, while the current domestic and foreign markets only 5N, 6N molybdenum powder is only in the laboratory small test stage, not industrial production, far from meeting the market demand. The research of high purity molybdenum powder will face great challenges in the future. Firstly, the raw material molybdenum ore from different sources, impurity composition is complex, the lack of a set of systematic and complete standards for the removal of impurities, we urgently need to different molybdenum raw materials and impurity composition, according to the characteristics of the impurity elements and their differences with the molybdenum, the establishment of a set of systematic and complete purification technology system; Secondly, high purity molybdenum preparation of the environment is very high, so it is necessary to improve the purity of the production environment, the use of chemical reagents, gases, production equipment and Finally, the development of high-purity molybdenum preparation technology can not be separated from the reliable detection means, the existing inductively coupled plasma mass spectrometry (ICP-MS) and glow discharge mass spectrometry (GDMS) can still meet the requirements for the detection of the relevant solutions and high-purity metal solids in the production, but with the further improvement of the purity of the trace elements still need to be developed with lower detection limits of the detection technology. Developing low-cost, green and efficient purification methods, proposing more efficient design solutions for impurity removal, and preparing high-purity molybdenum materials with higher purity and more stable quality will be our common needs in the future.
Spherical molybdenum powder prepared by Stardust's RF plasma spheroidisation powder making equipment has high purity, low oxygen content, high sphericity, smooth surface, no satellite balls, very few hollow particles, uniform particle size distribution, excellent flowability performance, high bulk density and taper density. It is widely used in contact materials, aerospace high temperature resistant components, targets and other fields. Spherical molybdenum powder is suitable for laser/electron beam additive manufacturing, laser direct deposition, hot isostatic pressing, injection moulding, laser cladding and other processes.
Hotline: +86 13318326187 Manager Zheng
Reference: Volume 48, Issue 3, June 2024, Molybdenum China, DOI : 10. 13384/j. cnki. cmi. 1006 - 2602. 2024. 03. 001
CCS : TG142. 71 Literature identification code : A Article number : 1006 - 2602(2024)03 - 0001 - 07