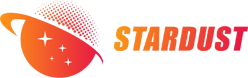
Ta10W is an important member of the tantalum-tungsten alloy family, its melting point is as high as 3080 ℃, the density of 16.78 ~ 16.90g/cm3, has a very good room temperature and high temperature mechanical properties, at a high temperature of 2,000 ℃, its tensile strength can still reach 100MPa, with good welding properties and high-temperature creep resistance [1-3].
Due to the Ta10W alloy has good ductility, weldability and excellent corrosion resistance, high temperature toughness, impact resistance, suitable for high temperature, high pressure, corrosion resistance and other working environments, in the aerospace, chemical, atomic energy industry and other aspects of the application is very wide, is the combustion chamber of the cosmic vehicle, the missile engine nose vertebrae, nozzles, exhaust pipes and other important high temperature parts of the preferred materials [4-6].
Ta10W alloy has good high-temperature mechanical properties, but its high-temperature antioxidant performance is poor, in the absence of protective measures, Ta10W alloy and other high-temperature alloys, as in 500 ℃ will appear ‘pest’ oxidation phenomenon. In the high-temperature alloy surface with high-temperature antioxidant coating can significantly improve the high-temperature oxidation resistance of the alloy, but also can maximise the retention of high-temperature strength of the alloy, the high-temperature alloy at high temperatures in the oxidation of the formation of a good protection.
1 experimental content and method
1.1 coating preparation
Preparation of coating substrate selection of tantalum tungsten alloy (Ta10W), test specimen size processing specifications for 70mm × 8mm × 1mm specimen, specimen by grinding, polishing, acid washing and drying spare.
Coating substrate MoSi2-TiB2-Zr as the main body, add functional elements according to a certain mass ratio after mixing, add ethanol as a solvent loaded into the ball mill jar, ball mill grinding coating slurry, coating slurry sprayed on the surface of the alloy specimen, and then sintered in a vacuum resistance furnace, the coating substrate is prepared. With the same method to Si-W-Hf as the main body, according to a certain mass ratio of functional elements added to the ethanol ball mill to prepare the coating slurry, the resulting coating slurry sprayed with the substrate and sintered in a vacuum resistance furnace to produce the coating surface layer, after two spraying and two sintering composite coatings are prepared.
1.2 Coating performance testing and methods
The antioxidant property of the coating is determined by endothermic method, selecting a high-temperature test bench, installing the specimen with the coating (70mm×8mm×1mm) on the test bench, heating the specimen with low-voltage and large current heating, and determining the temperature of the specimen with a MR two-colour infrared thermometer. When determining the static antioxidant performance of the coating, the temperature of the specimen is controlled by adjusting the output of current and voltage, and the specimen is raised to the test temperature in the atmospheric environment and then kept warm, when the specimen shows small black spots visible to the eye, it indicates that the local coating has already failed and the test is stopped. The time from the beginning of the insulation to the coating failure is the static high-temperature antioxidant life of the coating.
1.3 Organisational structure of the coating
Figures 1 and 2 give the morphology of the micro surface structure and cross-section structure of the SEM coating. As can be seen from the figure, the microstructure of the coating is honeycomb diffuse vitreous (honeycomb coating structure has excellent self-healing properties), the coating microstructure is complete and uniformly distributed, and there are no defects such as coating breakage and coating vacancies. The coating structure is dense, the diffusion layer is obvious, the thickness of the diffusion zone is uniform, the combination of the overall coating and the substrate is tight, and the thickness is uniformly distributed.
Fig. 1 Surface microscopic morphology of composite coating
Figure 2 Microstructure of composite coating cross-section
2 Test results and analysis
2.1 Coating principle
According to the metal and non-metal in the plasticity and antioxidant performance on the complementary, the choice of Si as a co-solvent, configuration with antioxidant, easy to diffuse, easy to solidify and other performance characteristics of the monomers or alloy powders, add binder, through the melting and burning of the metal surface to form a diffusion of solidified semi-ceramic body, so that in the high temperature atmospheric environment, the surface of the coating and the combination of oxygen to form a layer of dense vitreous enamel, the alloy substrate play a role of antioxidant. The role of the alloy substrate to play an antioxidant.
Coating structure mainly consists of four layers: the first barrier layer for the outer oxide layer, usually oxide, blocking the intrusion of external oxygen, the main function of the anti-temperature oxidation; the second barrier layer for the bonding of the main layer, the main body of the coating. At high temperatures, the main body of the coating has a dual role, its outer surface partially replenishes the oxidation layer volatilised elements, gradually forming the oxidation layer volatilisation, the inner surface layer blocks the third layer of elemental leaps and compensates for, and reinforces, the reinforcement layer; the third barrier layer, for the reinforcement layer, whose role is to block the alloy in the interstitial elements of the diffusion of the migration of the role of one or two layers, can effectively prevent the base material strength reduction caused by the depletion of the alloy interstitial elements The fourth layer is the diffusion layer, which is mainly to make the interaction between the alloy and the coating in a state of dynamic equilibrium, play the role of solidifying the coating and the alloy, and regulate the matching of the thermal expansion coefficient of the coating and the alloy. The four-layer structure of composite coatings, so that the coating and tantalum-tungsten alloy thermal expansion coefficient match well, the coating has good high-temperature antioxidant performance, while the mechanical properties of the alloy base material can be retained.
2.2 High temperature performance of the coating
Ta10W alloy composite coating static high-temperature antioxidant performance test, the results are: Ta10W alloy composite coating at 1800 ℃ after 25h of continuous work, the high-temperature zone of the coating specimen failure, the substrate loses its protection, and oxidises rapidly. Defects appeared on the surface of the coating after 5h of continuous work at 1950℃. The composite coating selects MoSi2-TiB2-Zr main coating material with good compatibility with tantalum-decatungsten alloy as the bottom layer, and Si-W-Hf main coating material with good high-temperature antioxidant performance as the top layer, which comprehensively improves the bonding strength and antioxidant capacity of the coating.
Fig. 3 Surface morphology of the coating in the failure area after high temperature test
Observe the morphology of the coating in the failure area (Figure 3, Figure 4), from the failure area coating surface and cross-section morphology can be seen, the failure area coating surface cavities, the surface glaze ceramic vitreous protective layer is completely destroyed, the inner layer of the coating began to oxidise, with the increase in oxidation time, the internal structure of the coating changes, in the thermal stress and the composite effect of the volatile gases within the coating internal pores continue to extend and expand, which ultimately led to the oxidation failure of the coating. Expansion, ultimately leading to oxidation failure of the coating. The reason for the destruction of the local surface glazed ceramic vitreous protective layer may be related to the active oxidation of SiO2 to generate gaseous SiO volatilisation loss or coating composition segregation.
Fig. 4 Cross-sectional morphology of the coating in the failure area after high temperature test
2.3 Coating failure analysis
Silicon coating is a kind of self-consuming coating, in the coating work, the coating surface of the Si element oxidation to form SiO2 and other elements of the oxide together to form a dense barrier layer, to protect the alloy substrate from being oxidised. The oxidation mode of the coating is divided into active oxidation and passive oxidation, passive oxidation mode is characterised by silicon and oxygen selective reaction, the formation of SiO2 and a low-value silicide product; active oxidation mode characteristics like a general reaction, the formation of silicon and metal oxides at the same time, or due to the lack of oxygen pressure, preventing the formation of SiO2 or prompting the decomposition of SiO2 into a gaseous product, SiO, which makes the coating of Si elemental loss increases and the rate of loss accelerates, which in turn shortens the coating life. At the same time, active oxidation will make a variety of metal elements in the coating to generate gaseous oxides, and these gaseous oxides will cause the coating organisation to be loose and rupture in serious cases, which will significantly shorten the antioxidant performance of the coating.
Coating in the high temperature test to a certain extent, due to the volatility of the coating at high temperatures, the coating surface layer will be thinned and loosened, or even missing, hollow and other defects, which provides a channel for the invasion of oxygen elements, due to the surface layer can not play a role in isolating the role of oxygen, the coating began to seepage of oxygen, which is oxidised to form the metal component of the metal oxides and the volume of expansion exacerbated by the coating structure of the loosening of the coating to accelerate the rate of oxidation of the coating. The oxidation rate of the coating is accelerated. As a result of the combined effect of these reactions, ultimately leading to coating failure. In addition, the coating is subjected to high temperatures, due to differences in thermal expansion coefficients between the coating and the substrate, the coating will produce small cracks, oxygen will follow these small cracks in the coating from the outside to the inside of the oxidation of the expansion, resulting in the formation of penetrating oxidative corrosion zone, with the corrosion of the spread of the aggravation of the coating eventually lead to failure.
3 Conclusion
①Taking MoSi2-TiB2-Zr and Si-W-Hf as the main body, by adding functional elements and adopting the slurry melting and burning method, a four-layer structural silicide composite coating with uniform structure and dense organisation can be prepared on the surface of tantalum-tungsten alloy by the method of two coats and two melting and burning, with the first layer as the oxidation layer, the second as the main body of the coating, and the third as the reinforcement layer; The fourth layer is the diffusion layer. ② By adding a layer of ‘reinforcement layer’ on the basis of the classical three-layer antioxidant coating structure, the mutual diffusion of elements between the coating and the alloy at high temperature is reduced, and the performance degradation of the alloy and the coating due to compositional changes is avoided. The composite coating can work continuously at 1800℃ for 25h and 1950℃ for 5h.
Reference: tantalum alloy high temperature antioxidant composite coating preparation research - Baidu Academic (baidu.com)
Stardust's spherical Ta-10W alloy powder has excellent high temperature and corrosion resistance for aerospace and electronics applications. Its uniform spherical particles improve flowability and densification, making it suitable for advanced manufacturing processes such as 3D printing and hot isostatic pressing. This alloy powder not only enhances product performance, but also meets high industrial standards.
Welcome to consult Manager Cathie Zheng +86 13318326187