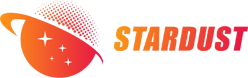
Abstract: The high carbon niobium tungsten alloy HCNb521 sintered bars were subjected to secondary electron beam melting to control the carbon, zirconium and gas content of the alloy. The microstructure of the smelted ingot after high temperature annealing was analyzed, and the mechanical properties of high carbon niobium tungsten alloy HCNb521 and ordinary niobium tungsten alloy Nb521 plates were compared. The research results show that the increase in carbon content causes more secondary strengthening phases to form in the niobium tungsten alloy, which improves the strength of the niobium tungsten alloy; electron beam melting can effectively control the composition content of the niobium tungsten alloy ingot; the material mechanical properties of high carbon niobium tungsten alloy are slightly improved compared with ordinary niobium tungsten alloy.
1 Introduction
Materials are the foundation of aerospace industry. With the continuous development of the aerospace industry, the market demand for high temperature alloys has diversified, and higher requirements have been put forward for their practical application and performance. The earliest studied high-temperature alloys were used in the turbine combustion chamber of aerospace engines. High-carbon niobium-tungsten alloy HCNb521 is a high-temperature alloy developed on the basis of niobium-tungsten alloy (Nb521, Ni-5W-2Mo-1Zr). The high-temperature use temperature has been greatly improved, and the adhesion of the high-temperature anti-oxidation coating (molybdenum silicide) used on the niobium-tungsten alloy has been greatly improved [1,2]. This alloy is obtained by two electron beam melting and then extrusion process to obtain the extruded billet for subsequent processing, and then through forging and rolling process to obtain qualified plate and bar products.
At present, many developed countries have put forward higher requirements for engines, with increased thrust-to-weight ratio, reduced number of parts, increased part life, and increased durability, so the requirements for the materials used are more stringent. The application of niobium-tungsten alloy has increased the working temperature of the thrust chamber to 1550 ℃, so that it can be better used in the aerospace industry. This paper studies the microstructure and properties of high carbon niobium tungsten alloy, which makes the performance of niobium tungsten alloy better. It is not only used in the high temperature thrust chamber of the engine, but also widely used in other high-speed aircraft. It is a new breakthrough in the application of high temperature niobium alloy.
2 Experiment
2.1 Raw materials
The raw materials of this experiment are high carbon niobium tungsten alloy sintered bars, and their main chemical composition is shown in Table 1.
2.2 Experimental process
The qualified high carbon niobium tungsten alloy sintered bars were prepared according to the proportion of gas and metal content, and the sintered bars were welded with an argon arc welding box to make electrodes. The electrode manufacturing specifications were 100 mm×100 mm×1500 mm. In order to make the composition of the high carbon niobium tungsten alloy more uniform, a 500 kW electron beam furnace (EB) was used for two smeltings. The diameter of the first smelting ingot was 160 mm, and the diameter of the second smelting ingot was 220 mm. Electron beam melting can effectively control the content of gas and impurities, and has a good purification effect on niobium tungsten alloy ingots, but its disadvantage is that the central grains of the smelting ingots will grow along the vertical axis, and the central grains are often coarse. The traditional arc melting method is beneficial to the alloy homogenization of the material, but increases the gas content of the alloy (the oxygen content of the first smelting increases by about 60×10-6).
The electron beam secondary melting ingot is machined for surface treatment to remove the pores and various melting defects generated during the melting process on the surface of the ingot. Then, it is covered with 3mm thick 45# steel, placed in a heating furnace, heated to 1270℃ and kept warm for 5-8min, and then transferred to a hot extruder for hot extrusion at an extrusion rate of 300mm/s and an extrusion ratio of approximately 4 times to obtain a D120mm finished extruded ingot.
2.3 Sample testing instruments
GQ-2ES carbon and sulfur high-speed analyzer, CAAM-2001 atomic absorption spectrophotometer, NovaNannoSEM scanning electron microscope, and room temperature and high temperature stretching machines.
3 Results and analysis
3.1 Chemical composition of ingot
The main chemical composition of the upper, middle and lower parts of the high carbon niobium tungsten alloy double smelting ingot was analyzed, and the results are shown in Table 2. Comparing the data in Table 1 and Table 2, it can be seen that the carbon and zirconium contents in the alloy after electron beam melting significantly decrease with the increase in the number of melting times, while the contents of tungsten and molybdenum change very little and can be ignored during the melting process. Since electron beam melting is a metal purification process, the oxygen content in the high carbon niobium tungsten alloy bar is basically determined to meet the requirements [1].
3.2 Microstructure of ingot
The microstructure of ordinary niobium tungsten alloy Nb521 and high carbon niobium tungsten alloy HCNb521 after the same high temperature heat treatment (1320 ℃×90min) is shown in the attached figure. The strengthening phases of carbides in high carbon niobium tungsten alloy are dispersed (Nb, Zr) C and Nb2C. The carbides of the material are calibrated by X-ray diffraction method, and the result shows that ZrC plays a strengthening role in high carbon niobium tungsten alloy [2]. The precipitation amount of carbides is different at different temperatures and the same holding time, which greatly improves the high temperature strength of the material. The following experiment was conducted on high carbon niobium tungsten alloy (HCNb521): high temperature annealing treatment was carried out in stages under the conditions of slab thickness of 7mm and finished product thickness of 1mm. High temperature annealing in stages during alloy processing can obtain a homogenizing heat treatment effect; as the processing rate increases, the annealing time gradually shortens, which can promote the uniform distribution of the dispersion strengthening phase. As can be seen from the attached figure, under the same heat treatment conditions, high carbon niobium tungsten alloy HCNb521 and ordinary niobium tungsten alloy Nb521 are both incompletely crystalline, and high carbon niobium tungsten alloy can more clearly see fine carbides distributed on the grain boundaries. These carbides play a role in pinning grain boundaries and dislocations during high temperature deformation, thereby improving the high temperature strength of the plate [3].
3.3 Mechanical properties of high carbon niobium tungsten alloy processed materials
The mechanical properties of high carbon niobium tungsten alloy HCNb521 plate and ordinary niobium tungsten alloy Nb521 plate obtained in the experiment are shown in Table 3.
From the data in Table 3, it can be seen that the performance difference between the two is not very large. The strength of high carbon niobium tungsten alloy is slightly improved, and the tensile strength and yield strength are higher than those of materials such as C-103 niobium hafnium alloy, which is beneficial to increase the use temperature of the combustion chamber [4].
4 Conclusion
(1) The increase of carbon content makes more secondary strengthening phases form in niobium tungsten alloy, and the strength of niobium tungsten alloy is improved.
(2) Electron beam melting of niobium tungsten alloy ingot can effectively control the composition content of ingot.
(3) The mechanical properties of the material obtained by high carbon niobium tungsten alloy plate are slightly improved.
Paper citation information
Volume 44 No. 1
February 2016
Rare Metals and Cemented Carbides
Rare Metals and Cemented Carbides
Vol. 44 No. 1
Feb. 2 0 1 5
Niobium tungsten alloy Nb521 material has excellent room temperature and high temperature mechanical properties and the advantages of high melting point, low density, high strength at high temperature and good machinability.
The spherical Nb521 alloy powder produced by Stardust Technology is prepared by radio frequency plasma spheroidization process, which has the characteristics of high purity and low oxygen, high sphericity, smooth surface, no satellite, uniform particle size distribution, excellent flowability, high loose density and high tap density.
Niobium tungsten alloy Nb521 is widely used in the manufacture of aerospace engines, weapon thrusters, rocket missile liquid bicomponent engines, nuclear reactors, submersibles, gas turbines, automobile engines, diesel engines, high temperature furnace heating belts, high temperature molds, high temperature fixtures, and high temperature crucibles.
For more details, please contact Vicky+86-13318326185