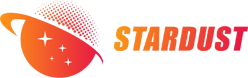
The process test was carried out to explore the process parameters of electron beam welding of Nb521 material and the mechanical properties of welds at different temperatures, to obtain the welding processability evaluation of the material and accumulate data for the engineering application of the material.
1 Experimental plan
1.1 Experimental materials
The Nb521 niobium tungsten alloy plates and bars are in a recrystallized state, and the chemical composition is shown in Table 1.
1.2 Process preparation before welding
In order to ensure the quality of the weld and more effectively eliminate the oil stains and residual metal chips at the weld, pickling and mechanical grinding are usually used to treat the parts before welding, and wipe them clean with anhydrous ethanol or acetone.
2 Test methods and results
2.1 Electron beam welding test plan and results
In order to avoid cracks and pores in Nb521 alloy electron beam welding, the following measures are taken: strengthen pre-welding cleaning, reduce heat input during welding by optimizing the matching of parameters such as electron beam current, acceleration voltage, welding speed, focusing current and working distance, control weld shape, reduce stress concentration, thereby achieving the purpose of refining weld structure and reducing welding stress, and finally eliminating pores and cracks. The rationality of the parameters is preliminarily judged by weld formation, and the main welding process parameters are shown in Table 2.
2.2 Analysis of surface quality of electron beam welding test pieces
A pair of test pieces are welded using the parameters in Table 2, and the surface morphology is shown in Figure 1. It can be seen that the front width of the weld is 4.5~5.0 mm, the back width of the weld is 2.0 mm, and the excess height is 1.0 mm. The surface quality can meet the requirements of Class I welds in GJB1718A-2005 "Electron Beam Welding".
2.3 X-ray detection
To check whether there are cracks, pores, unfused defects in the welded joint, X-ray detection is performed on it. When the weld is cleaned before welding and the process parameters are matched, the electron beam welded joint meets the requirements of Class I welds in GJB1718A-2005.
2.4 Analysis of mechanical properties at room temperature
To detect the mechanical properties of the weld at room temperature, the electron beam welded test piece is made into a tensile specimen and tested using a WDW-100 microcomputer-controlled electronic universal testing machine. The measured data are shown in Table 3, and the morphology of the tensile specimen after fracture is shown in Figure 2.
From the test results, the tensile strength and yield strength of the electron beam weld of Nb521 niobium alloy can reach more than 95% of the parent material, and the elongation reaches 86.7% of the parent material, and the welding quality is good.
2.5 Analysis of high temperature mechanical properties
In order to detect the tensile performance data of the weld at different high temperatures such as 600 ℃, 800 ℃, 1 000 ℃, 1 200 ℃, 1 400 ℃, 1 600 ℃, and 1 800 ℃, the tensile specimens of the electron beam welded specimens were tested on the WDW-100 microcomputer-controlled electronic universal testing machine. The measured data are shown in Table 4, and the high temperature tensile fracture specimens are shown in Figure 3.
According to the test results in Tables 3 and 4, the relationship between the tensile strength, yield strength, and elongation of the electron beam weld at different temperatures is shown in Figure 4. It can be seen that with the increase of temperature, the tensile strength and yield strength of the electron beam weld both show a downward trend. Compared with room temperature, the tensile strength and yield strength of the weld decrease faster at 600 ℃, while the change is relatively gentle at 600~1 000 ℃, and decreases at the same gradient at 1 000~1 800 ℃. As the temperature rises to 1 600 ℃, the elongation of the electron beam weld increases, but at 1 800 ℃, the elongation drops to the minimum. This is mainly because the specimens are broken in the parent material or heat-affected zone before 1 600 ℃, while the tensile specimens are broken at the weld at 1 800 ℃.
2.6 Metallographic test analysis
The overall morphology of the electron beam weld of Nb521 niobium alloy is shown in Figure 5. As shown in Figure 5, the weld forms a layered structure, the edge of which is a joint structure, followed by columnar crystals with strong directionality. This is mainly because when electron beam welding Nb521 niobium alloy is used, the welding heat input is large, the cooling speed of the molten pool is fast, and the weld forms columnar crystals with strong directionality. After modified welding, the columnar crystals are reduced. The structure of the weld center is shown in Figure 6. It can be seen that the weld center is an equiaxed columnar crystal structure, and a large number of carbide strengthening phases are precipitated on the equiaxed crystals. This is mainly because there are many carbides such as MC, M2C and M3C2 in niobium tungsten alloy. The fine and stable carbides, nitrides and oxides are dispersed phases for niobium alloys. It is the most effective high-temperature strengthening method. With the high-temperature melting during electron beam welding, the strengthening phase begins to precipitate and aggregate and grow. As the high-temperature strengthening phase of niobium tungsten alloy, carbides can only play a good high-temperature strengthening role when they are dispersed, but their aggregation and growth will lead to a decrease in the high-temperature strength of niobium tungsten alloy. The weld heat affected zone structure is shown in Figure 7. It can be seen that the joint heat affected zone produces local melting and grain growth along the grain boundary, forming coarse grain bands on both sides of the weld, which directly affects the tensile properties of the joint. Figure 8 shows the material matrix structure, which is uniform and delicate, and is an equiaxed crystal structure.
2.7 Fracture Scanning Electron Microscope Analysis
The tensile fracture of the samples in the 1200℃ and 1800℃ tensile tests was observed and analyzed by scanning electron microscopy, and the results are shown in Figures 9 and 10. As shown in Figure 9, the fracture morphology of the sample at 1200℃ is a ductile fracture, and there are a large number of dimples on its surface. Therefore, the material has a strong tensile strength. In the fracture of Figure 10, there are a large number of clearly visible grains, which is an intergranular fracture morphology. There is a smooth surface without bonding force on the fracture surface, which is a brittle fracture morphology. The tensile strength is weak, and the weld fractures brittlely at 1800℃. Therefore, the material should be used at less than 1600℃.
3 Conclusion
(1) The room temperature tensile strength and yield strength of Nb521 niobium alloy electron beam weld can reach more than 95% of the parent material, and the elongation reaches 86.7% of the parent material, and the welding quality is good.
(2) With the increase of temperature, the tensile strength and yield strength of Nb521 niobium alloy electron beam weld both show a downward trend. The tensile strength and yield strength of electron beam welds change relatively slowly at 600~1000℃, and decrease at the same gradient at 1000~1800℃; the extension of electron beam welds first shows an increasing trend, and the elongation drops to the minimum at 1800℃.
About Stardust Technology
Stardust Technology (Guangdong) Co., Ltd. is a national high-tech enterprise specializing in the research, development, production and sales of high-end spherical powder materials for 3D printing, powder metallurgy, surface engineering and other fields. The company insists on taking radio frequency plasma spheroidization powder making technology as the core, and provides internationally advanced powder products and application solutions.
The company's main products include high-end rare refractory metals such as tungsten, molybdenum, tantalum, niobium, vanadium, rhenium, chromium and their alloys, compound spherical powders, and also provides technical services such as radio frequency plasma spheroidization, plasma rotating electrode atomization, 3D printing, hot isostatic pressing, injection molding, powder metallurgy, etc.
Niobium tungsten alloy Nb521 material has excellent room temperature and high temperature mechanical properties and the advantages of high melting point, low density, high temperature and high strength and good machinability. The spherical Nb521 refractory alloy powder produced by Stardust Technology is made by radio frequency plasma spheroidization atomization method. It has the characteristics of high purity oxygen deficiency, high sphericity, smooth surface, no satellite, uniform particle size distribution, excellent flow performance, high loose density and vibration density. Niobium tungsten alloy Nb521 is widely used in the manufacture of aerospace engines, weapon thrusters, rocket missile liquid bicomponent engines, nuclear reactors, submersibles, gas turbines, automobile engines, diesel engines, high temperature furnace heating belts, high temperature molds, high temperature fixtures, and high temperature crucibles.https://www.stardustpowder.com/niobium-tungsten-alloy15-53mm
For more details, please contact us
Paper citation information
Volume 51 No.4 Apr. 2021 Electric Welding Machine
Chinese Library Classification Number: TG456.3 Document Code: A Article Number: 1001-2003(2021)04-0090-05
DOI: 10.7512/j.issn.1001-2303.2021.04.18