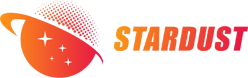
3D printing technology is an additive manufacturing technology that can quickly reach high temperatures so that the sample reaches the sintering temperature. It is not limited by the original shape of the mold. It can prepare parts with complex shapes with high processing accuracy and avoid subsequent machining to bring defects to the product. It has the advantages of eliminating defects and is widely used in biomedicine, aerospace and other ultra-precision devices, industry, construction, archaeology and other fields. 3D printing has high requirements for raw material powders. Generally, it requires high powder purity, good sphericity, narrow particle size distribution range, low oxygen content, etc. to ensure smooth powder spreading and good performance of printed products. When using irregularly shaped powder for 3D printing, the powder fluidity will be significantly reduced, causing problems such as reduced powder layer density and uneven powder distribution. There are many methods for preparing spherical powders, among which plasma spheroidization technology has received widespread attention because it can significantly improve the sphericity of particles and reduce the impurity content of powders. In addition, thermal plasma has a high temperature and a fast cooling rate, and is suitable for spheroidizing high-melting-point metals and alloy powders, broadening the range of applicable materials for 3D printing. The emergence of 3D printing technology provides a new idea for the preparation of refractory metal materials, making it possible to quickly prepare refractory metal products with complex shapes. In recent years, various scientific research institutions and high-tech companies at home and abroad have attached great importance to the application of 3D printing technology in the field of refractory metals such as tungsten and molybdenum, and have begun to explore. In 2018, Ravi K. Enneti and others explored the process parameters for preparing tungsten products using selective laser melting technology. The experimental results showed that the parameters were set to a laser power of 90W, a powder coating thickness of 30μm, and a scanning rate of 200~1400mm/s. , tungsten products with relative densities in the range of 59% to 75% can be produced. In China, Xie Yanjun’s team at the General Institute of Iron and Steel Research used selective laser melting technology and set the laser power to 300W to prepare a pure tungsten block sample with a relative density of 97%. Since the melting point of molybdenum (2620°C) is higher than that of general metals, but lower than that of tungsten (3410°C), inappropriate process parameters can easily lead to insufficient sintering of molybdenum products or evaporation loss of metal molybdenum, reducing the overall performance of molybdenum products. It is particularly important to select appropriate 3D printing technical parameters. However, the research on using 3D printing technology to process and produce pure molybdenum products is still blank in China. Studies have shown that 3D printing can cause defects such as holes and cracks, and these morphological features are mainly affected by laser power and scanning rate. Therefore, this article uses selective laser melting technology to 3D print molybdenum powder. It mainly studies the effects of changes in laser power and scanning rate on the performance and internal defects of pure molybdenum blocks prepared by selective laser melting, and promotes 3D printing in refractory materials. Applications in the field of metals.
1 Experimental materials and methods
1.1 Experimental methods
1.1.1 Plasma spheroidization technology
In order to meet the raw material requirements for 3D printing, in this experiment, before 3D printing, the raw molybdenum powder with small particle size was first pretreated to increase the original molybdenum particle size, and then plasma spheroidization technology was used to optimize the physical properties of the powder to obtain The schematic process diagram of spherical molybdenum powder for 3D printing is shown in Figure 1. Plasma spheroidization technology uses gas to carry metal powder and spray it into the plasma torch through a feeding gun. The powder particles quickly absorb heat and melt, and condense into spherical droplets under the action of surface tension. After instantaneous cooling and solidification, spherical powder is prepared.
The surface morphology and cross-sectional morphology of molybdenum powder after plasma spheroidization are shown in Figure 2, and its physical properties are shown in Table 1. It can be seen from Figure 2 that after pretreatment and plasma spheroidization process, the original finely broken molybdenum powder turned into spherical particles with dense internal structure, regular shape, and relatively uniform size distribution. The powder oxygen content was low, and the bulk density and fluidity were improved. Significantly improved.
1.1.2 Selective laser melting technology
Selective laser melting technology first uses a computer to model the final sample and divide it into very thin layers. Each layer of powder is melted under the action of a computer-guided laser beam, and the process proceeds layer by layer. Due to the Rayleigh length of the incident laser beam and thermal conduction, solidification bonding occurs between two adjacent layers. This technology directly achieves the purpose of molding by melting and solidifying the powder. In the selective laser melting process, the laser acts on the powder for a short time. The process is very complex, including heat transfer, mass transfer and chemical reactions. This experiment uses selective laser melting as a technical means and adjusts the two process parameters of laser power and scanning rate to prepare refractory metal molybdenum blocks of the same size.
1.2 Detection method
In this experiment, the D1347 solid density meter was used to measure the density of the sample, and the 402MVA automatic turret micro-Vickers hardness tester was used to measure the hardness. The powder micromorphology and the cross-sectional morphology of 3D printed products were analyzed under a HITACHI SU5000 scanning electron microscope. The sample was moderately corroded. The etching solution formula was K3[Fe(CN)6]:NaOH:H2O = 1:3:16 (g). After etching under a microscope, the surface morphology of the sample was observed.
1.3 Experimental materials
The raw materials used in this experiment are shown in Figure 2. Figure 2(a) shows the morphology of the original molybdenum powder, and Figures 2(b) and (c) show the molybdenum powder for 3D printing obtained after pretreatment and plasma spheroidization respectively. Microscopic morphology and cross-sectional morphology. The physical properties of molybdenum powder for 3D printing are shown inTable 1.
2 Results and discussion
2.1 Laser energy density
Research shows that the densification process, the number of pores and the formation mechanism of defects in 3D printing materials are related to the laser energy density. Laser energy density (LED), also called body energy, can be expressed by formula (1):
2.2 Effect of laser power on the performance of molybdenum products
In order to explore the effect of laser power on the performance of molybdenum products, the process parameters were set to 70W, 80W, 90W, and 100W respectively before selective laser melting. Other process parameters are the same, the scanning rate is 400mm/s, and the pitch is 0.08mm. Measure the substance of the sample obtained Rational performance, the results are shown in Table 2. It can be seen from the table that as the laser power increases, the density of molybdenum products gradually increases. When the laser power is 100W, the density reaches a maximum of 9.543g/cm³. At the same time, the microhardness of the sample also improved to a certain extent as the laser power increased.
The cross-section of the sample was polished and placed under a scanning electron microscope for morphological observation. Figure 3 shows the SEM image of the cross-section of the sintered body after sintering with different laser powers. It can be seen from the figure that when the sintering power is 70W, the connected pores inside the sample are larger in size, more in number, and evenly distributed on the cross section. Some particles are not bonded to each other and are in an independent state, as shown by the areas marked by circles in Figure 3(a) and (b). As the laser power increases, the closed pores inside the 3D printed molybdenum block gradually appear, and the number gradually increases. It can be seen from formula (1) that when other parameters are fixed, the laser energy density increases with the increase of laser power. When the power is 70W and 80W, the energy provided by the laser beam is not enough to fully melt and bond the molybdenum particles, and the microstructure is not dense, resulting in low density and poor physical properties of molybdenum products. When the laser power continues to increase, the number of unmelted particles decreases significantly until they disappear completely. At the same time, the number of internal connected pores in molybdenum products decreases, and the proportion of closed pores becomes higher and higher. The formation of closed holes is due to the very high cooling rate of selective laser melting technology. Some of the dissolved gases in the liquid metal do not have time to escape before the metal solidifies, and remain to form pores inside the product, hindering further densification of the product. After comparison, when the laser power is 100W, the comprehensive performance of the prepared molybdenum products is better.
2.3 Effect of scanning rate on the performance of molybdenum products
Like laser power, scanning rate is also an important parameter that affects the effect of selective laser melting. Before selective laser melting starts, the laser power is set to 100W, the spacing is 0.08mm, and the scanning rates are 400mm/s, 500mm/s, 600mm/s, and 700mm/s. The density and hardness of the obtained samples were measured, and the results are shown in Table 3. According to Table 3, when the scanning rate is 500mm/s, the maximum density of molybdenum products is 9.82g/cm3, the relative density is 96.27%, and the hardness is 360.23HV. Subsequently, the density of molybdenum products gradually decreased with the increase of scanning rate, and the hardness values also showed a similar trend. In order to study the effect of sample scanning rate on the micromorphology of the sample, the obtained sample was observed by SEM, and the results are shown in Figure 4.
Prepare the corresponding etching solution, etch the cross-section of the sample, and observe the structural changes under a microscope. Figure 5 shows the microstructure of the sample after corrosion treatment. When the scanning rate is 400mm/s, there are many obvious cracks inside the molybdenum product. As the scanning rate increases, the number of cracks shows a downward trend. This is because metal molybdenum has poor plasticity. During the selective laser melting process, the sample cools quickly, and the molten molybdenum generates tensile stress during the heat shrinkage process. When the tensile stress exceeds the limit value of the material, the interior of the molybdenum product becomes unstable.
Cracks will appear, adversely affecting the performance of molybdenum products. When the scanning rate is 400mm/s, the laser energy density is maximum, and the molybdenum particles are fully melted by the higher energy of the laser beam. During the rapid cooling process, the metal molybdenum shrinks and generates tensile stress, resulting in Cracks appear.
When the scanning rate increases to 500mm/s, the laser beam energy is enough to fully affect the molybdenum products, and the number of internal cracks is reduced. At this time, the prepared molybdenum products have the highest density and highest hardness. When the scanning rate continues to increase, the laser beam has insufficient effect on the molybdenum products.
points, resulting in a significant decline in the performance of molybdenum products.
Conclusion
3D printing is different from traditional sintering processes in that it does not require molds, has high production efficiency, and is conducive to the production of parts with complex structures. Due to the high melting point of molybdenum, 3D printing of molybdenum and molybdenum alloys is difficult, so the study of process adaptability is particularly important. By conducting experiments to explore the process parameters of 3D printed molybdenum products, the following conclusions were reached:
(1) As the laser power increases, the laser energy density also gradually increases. As the energy transferred to the sample surface by the laser beam gradually increases, the number of internal pores in the molybdenum products prepared by selective laser melting gradually decreases, and the density gradually increases.
(2) Like laser power, scanning rate will also significantly affect the effect of selective laser melting. According to the laser energy density formula, laser energy density is inversely proportional to the scanning rate. When the scanning rate decreases, the energy density acting on the sample surface increases, and the particles inside the sample are fully melted and bonded. But for metal molybdenum, rapid cooling after full melting will cause cracks inside it, affecting the performance of the sample.
(3) When the process parameters are laser power of 100W, spacing of 0.08mm, and scanning rate of 500mm/s, the molybdenum products prepared from plasma spheroidized molybdenum powder as raw material have the best performance, with a density of 9.82g/cm³. The relative density is 96.27%.
The selective laser melting process is very complex. In this process, in addition to the laser power and scanning rate that will significantly affect the sample performance, other factors such as spacing will also have a certain impact on the sample performance. The influence of spacing and other factors on sample performance and the various factors The synergistic effects will be further explored in subsequent research.
About Stardust Technology
Stardust Technology (Guangdong) Co., Ltd. is a national high-tech enterprise specializing in the research, development, production and sales of high-end spherical powder materials for 3D printing, powder metallurgy, surface engineering and other fields. The company insists on taking radio frequency plasma spheroidization powder making technology as the core, and provides internationally advanced powder products and application solutions.
The company's main products include high-end rare refractory metals such as tungsten, molybdenum, tantalum, niobium, vanadium, rhenium, chromium and their alloys, compound spherical powders, and also provides technical services such as radio frequency plasma spheroidization, plasma rotating electrode atomization, 3D printing, hot isostatic pressing, injection molding, powder metallurgy, etc.
The radio frequency plasma spheroidization powder making technology (Radiofrequency Plasma Spheroidization Technology) adopted by Stardust Technology is to use carrier gas to introduce low-cost, irregularly shaped powders into plasma, and use the ultra-high temperature characteristics of plasma to quickly melt and cool the powder to achieve spheroidization and modification of the powder. This technology has unparalleled advantages over other powder making technologies in the preparation of rare refractory metals and compound spherical metal powders. This technology has the characteristics of wide adaptability of material system, multiple sources of raw materials, low cost, controllable particle size of spherical powder products, high powder sphericity, very few satellite balls and hollow powders, excellent flow properties and no electrode pollution. It is particularly suitable for large-scale production of high-end rare refractory metals and compound spherical powder materials. The metal powder prepared by this technology has become a recognized high-quality powder in the current advanced manufacturing fields such as additive manufacturing, aerospace and medical.
Please contact us for more details
Paper citation information:
Zhang Yuqing, Wang Luyan, Li Caobing, Research on the adaptability of plasma spheroidized molybdenum powder 3D printing process, Spraying Technology, Vol. 12, No. 2, June 2020.
Chinese Library Classification Number: TG174.4 Document Identification Code: A Article Number: 1674-7127(2020)06-0010-07, DOI 10.3969/j.issn.1674-7127.202