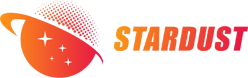
Basic Properties of Tantalum
Tantalum metal is silvery white with a density of 16.654 g/cm3. Its high density is related to relative atomic mass, atomic radius and atomic volume. The relative atomic mass of tantalum atom is about 180.95, the atomic volume is 10.9 cm³/mol, and the atomic radius is 0.146 nm. The relative atomic mass per unit atomic volume is large, so its density is high. Tantalum has a body-centered cubic lattice structure, with close arrangement of atoms and more slip systems, so tantalum has good elongation properties. The metal bonding energy between tantalum atoms is large, and the energy required to destroy the metal bonding is large, resulting in a melting point as high as 2997 °C. In addition, tantalum has a low expansion coefficient of about 7×10–6 ℃–1, which is lower than common metals such as gold, silver, aluminum, copper and iron.
Application of Tantalum in the Medical Field
The potential of tantalum in the medical field has received widespread attention. Figure 2(d) is a medical tantalum-titanium composite material. Tantalum as a coating can improve the biocompatibility of the alloy. However, there are differences in the properties of the coating and the substrate material. The surface modified coating usually exhibits poor bonding strength, and the coating is easily damaged during use, which limits its function. In the medical industry, using tantalum as the main raw material, that is, preparing all-tantalum bone implants, is an effective way to overcome the above shortcomings. However, due to the high melting point and high affinity for oxygen of tantalum, the traditional processing method is difficult to process, and the production efficiency and material utilization rate are low, which greatly increases the preparation cost of tantalum implants and increases the burden on patients. Therefore, a new process is urgently needed to achieve efficient and accurate forming of all-tantalum bone implants.
3D printing tantalum
3D printing is a new processing method. The most notable feature of this technology is that it can directly form the final three-dimensional sample according to the imported workpiece model. Laser Powder Bed Fusion (LPBF) and Electron Beam Melting (EBM) in 3D printing are often used to process tantalum implants. The schematic diagram of LPBF processing is shown in Figure 3. The LPBF processing equipment has three chambers, namely the powder chamber, the forming chamber and the recycling chamber. Metal powder needs to be added to the powder chamber in advance before printing. During processing, the powder is evenly spread in the forming chamber by a scraper, and then solidified into a pre-set shape after being melted and heated by a laser or electron beam. The powder chamber rises layer by layer, and the forming chamber descends layer by layer, and finally forms a layer by layer.
3D printing medical tantalum implant case
With the continuous improvement of medical level and the implementation of "Made in China 2025", new preparation processes represented by additive manufacturing have promoted the vigorous development of my country's orthopedic implant market. Since 2015, my country has become the world's second largest consumer of bone implants. At present, bone implant products can be divided into spine, joint and trauma categories according to the use scenario, among which acetabular cups (joint implants) and intervertebral fusion cages (spinal implants) have the fastest commercial development. Bone implant manufacturing materials include metals, ceramics, polymers and carbon materials. Among them, tantalum, as a member of metal bone implants, has great development potential.
Spinal products
Joint products
In 2022, Zhongshan Hospital Affiliated to Dalian University performed the world's first 3D printed tantalum metal ankle joint implant for a patient (Figure 9) [24]. The patient had talar necrosis and ankle inflammation. In order to solve the patient's pain symptoms and restore ankle flexibility, the hospital customized a 3D printed metal tantalum ankle joint for the patient. After the implant, the patient recovered well and could walk slowly one day after the operation.
Pelvic surgery has always been one of the difficult problems in orthopedic surgery. In 2022, Zhongshan Hospital Affiliated to Dalian University performed 3D printed tantalum hemipelvis and hip prosthesis implantation for a patient with right hip deformity caused by pelvic tumor (Figure 10(a)), further broadening the application of 3D printed porous tantalum. The patient had a large damaged area and needed to remove the ilium, acetabulum, and part or all of the pubic bone and ischium. The removal and implantation surgery was difficult. The hospital customized the implant for the patient through 3D printing, which was highly matched with the defective area after the patient's resection (Figure 10(b)), saving the implantation time.
Trauma products
In April 2019, the 3D printed trabecular tantalum stent developed by Xiangya Hospital was successfully implanted into a patient with femoral head necrosis. This was the world's first tantalum metal stent implantation surgery (Figure 11) [26]. The top of the tantalum stent is in an arc shape at the contact point with the human bone, which is similar to the curvature of the human bone. When the stent is subjected to force, there are many contact points with the human bone, and the pressure is relatively even, which can prevent the implant from being damaged.
3D printed tantalum powder-Stardust Technology
About Stardust Technology
Stardust Technology (Guangdong) Co., Ltd. is a national high-tech enterprise specializing in the research, development, production and sales of high-end spherical powder materials in the fields of 3D printing, powder metallurgy, surface engineering, etc. The company insists on taking radio frequency plasma spheroidization powder making technology as the core, providing internationally advanced powder products and application solutions.
Medical grade spherical tantalum powder
The spherical tantalum powder produced by Stardust Technology using radio frequency plasma spheroidization technology has excellent biocompatibility and bone ingrowth characteristics, and is widely used in 3D printing of clinical medical implants such as spine, joints, and trauma. Stardust Technology is the first in China to achieve an industrial breakthrough in medical-grade spherical tantalum powder. It has jointly promoted the clinical medical application of tantalum metal with domestic first-class orthopedic hospitals and medical device companies. It has participated in the formulation of GB/T 38975-2020 Tantalum and tantalum alloy powder for additive manufacturing, GB/T 41883-2022 Powder bed fusion additive manufacturing of tantalum and composite alloys, 2 national standards, YY/T1851-2022 Medical pure tantalum powder for additive manufacturing, 1 industry standard, T/CAMDI065-2021 Additive manufacturing of tantalum metal knee prosthesis, T/CAMDI 066-2021 Additive manufacturing of tantalum metal individualized bone defect filler "and other 3 group standards, and assisted in the completion of more than 500 cases of tantalum metal clinical application, implanted prostheses include tantalum metal intervertebral fusion bone spacers, hip joints, shoulder joints, knee joints, ankle joints, etc.
Welcome to inquire
Paper citation information:
Yang Zhenyu, Zhu Jiangqi, Yan Xingchen. 3D Printing Tantalum Medical Metal Materials[J]. Metal World, 2023 (6): 16-23. doi: 10.3969/j.issn.1000-6826.2023.10.0885