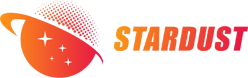
With the rapid development of aerospace technology, the performance requirements for rocket engines are getting higher and higher. Advanced manufacturing technology has become one of the key factors in improving the performance of rocket engines. SLM metal 3D printing, as an additive manufacturing technology with great development prospects, has been widely used in the aerospace field due to its unique advantages such as high design freedom, lightweight weight reduction, high material utilization, low production cost, shape integration, and the ability to manufacture complex internal structures, and has brought innovative impacts to it.
The engine is the core component of the rocket. As one of the most critical components of the engine, the rocket engine tail nozzle is responsible for converting the high-temperature and high-pressure gas generated by combustion into thrust. It needs to withstand the impact of high temperature, high pressure and high-speed airflow. Its structure is complex and precise, and its operating environment is harsh. It has extremely strict requirements on structure and material performance. Therefore, the tail nozzle needs to have extremely high temperature resistance, good thermal expansion coefficient and sufficient mechanical strength. At the same time, in order to improve the efficiency of the engine, the tail nozzle is often designed with complex cooling channels and lightweight structures.
The traditional rocket engine tail nozzle manufacturing process usually requires multiple processes, such as forging, machining, welding, etc., which is costly and has a long manufacturing cycle. Through SLM metal 3D printing technology, complex designs and integrated forming that are difficult to accomplish with traditional methods can be achieved, which greatly shortens the design, test and production cycle and greatly reduces production costs.
Taking a certain type of rocket engine tail nozzle as an example (non-confidential data), the structure has a diameter of about 510mm and a height of about 800mm. It has a complex structure and high forming requirements. The Sino-Swiss Technology team uses the iSLM600QN, a high-efficiency additive manufacturing system for aerospace mass production, to manufacture it while taking into account product quality and production efficiency. Through optimized design, it has achieved more complex internal cooling channels and internal lightweight weight-reducing structures, greatly improving the cooling efficiency and performance of the tail nozzle. At the same time, the use of IN718 high-temperature alloy materials with good high-temperature performance and mechanical strength ensures the durability of the tail nozzle in extreme environments.
iSLM600QN, a large-scale four-laser metal 3D printing device from Sino-Swiss Technology, adopts self-developed multi-laser scanning strategy and calibration algorithm, which can accurately and stably control and plan multi-laser scanning paths, ensure efficiency while achieving dynamic overlap, and ensure consistent performance of printed parts across the entire format; and through precise control and optimization of relevant parameters, as well as innovative optimization design of the wind field of the forming cabin, effectively ensure the density and surface quality of the rocket engine tail nozzle.
At the same time, due to the large size and complex structure of the rocket engine tail nozzle, the Sino-Swiss Technology technical team used the self-developed PCT600 powder cleaning machine to further clean and recycle the powder after the printing of the rocket engine tail nozzle, which greatly shortened the production cycle. , saving production costs. After testing, the performance of the tail nozzle has been significantly improved compared to conventionally manufactured tail nozzles.
The iSLM600QN equipment of Sino-Swiss Technology has successfully realized the integrated, lightweight and rapid manufacturing of rocket engine tail nozzles, which not only greatly reduced the number of parts, but also effectively improved the efficiency, performance, quality and reliability of the products, enabling new quality productivity in the aerospace industry.
Rocket engine tail nozzle (non-confidential data)
Printing process: SLM (selective metal melting)
Printing equipment: Zhongrui Technology iSLM600QN metal equipment
Printing material: nickel-based high-temperature alloy (IN718)
Layer thickness: 0.06mm
Part size: 508mm (X) × 508mm (Y) × 801mm (Z)
Printing time: 146 hours and 20 minutes
Surface treatment: sandblasting
Application field: aerospace
Zhongrui Technology iSLM600QN equipment is positioned for military and aerospace applications. The forming size is 600mm (X) × 600mm (Y) × 1000mm (Z, including substrate thickness). It is suitable for forming large-size, high-precision, and complex precision parts with harsh service conditions. It can fully meet the needs of high-end application fields such as aerospace for high-performance, high-efficiency, and high-quality parts for batch production and stability.
The original article comes from: Sino-Swiss 3D Printing